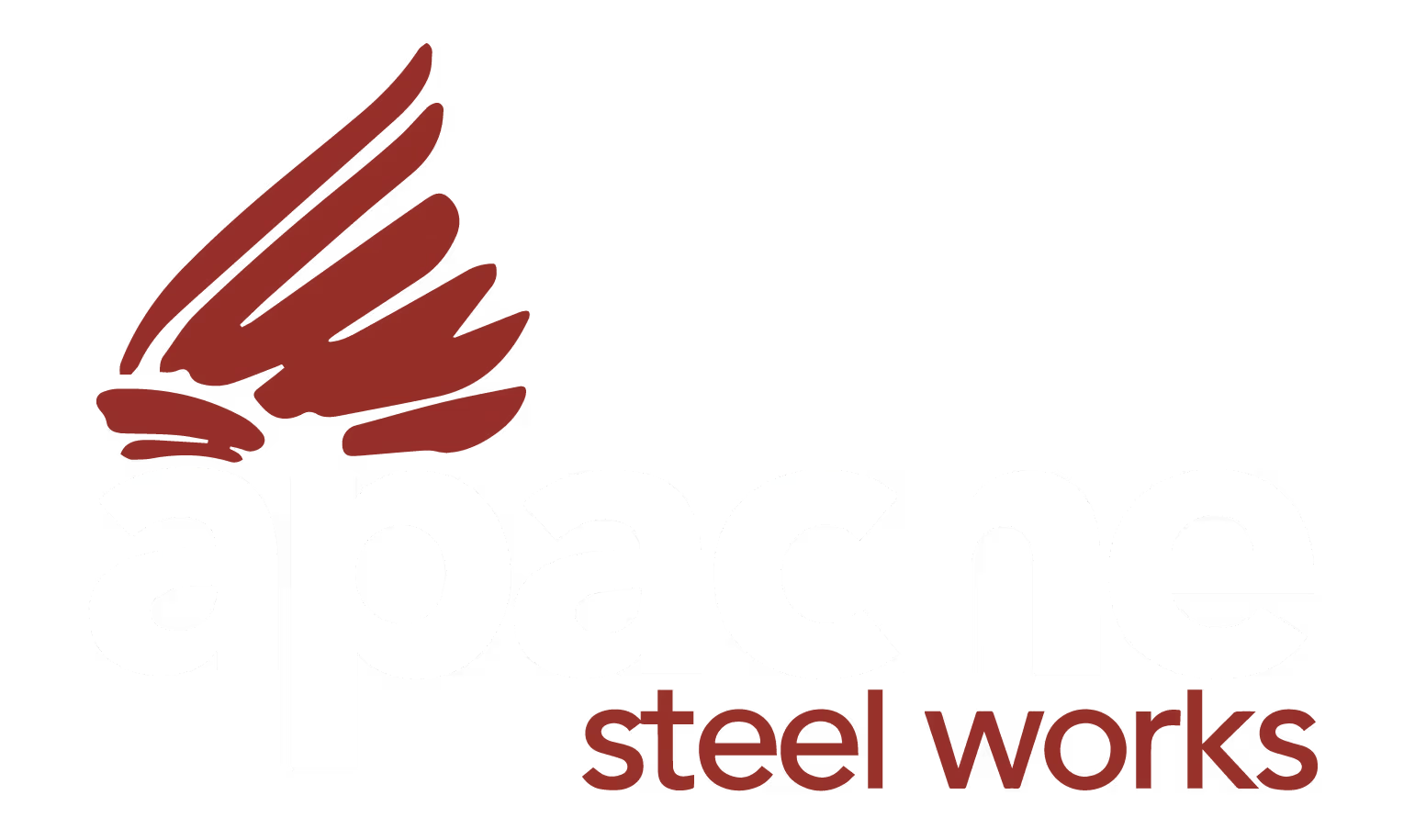
Plate Processing Company
Why does the metal plate have to be beveled? | Plate beveling solutions
Why does the metal plate have to be beveled? | Plate beveling solutions
Metal plates are used in many industries like construction, manufacturing, and fabrication. These plates often need to be beveled. Beveling is the process of creating an angled edge on the metal plate. This blog explains the reasons why plate beveling solutions in Houston are important when working with metal plates.
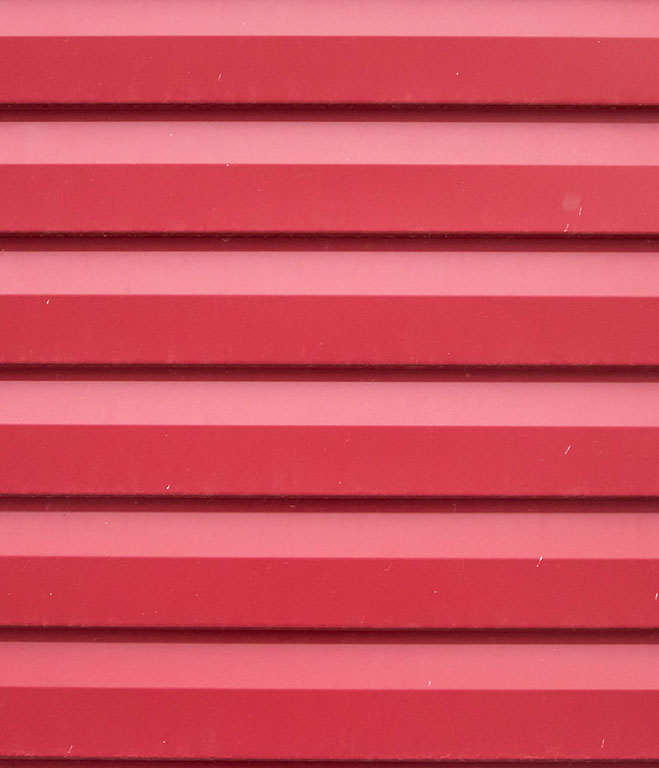
What is Beveling?
Beveling is the process of creating a slanted or angled surface along the edge of a metal plate. This is done by grinding away part of the metal plate's edge at an angle. The angle created is called the bevel angle. Common bevel angles range from 30-45 degrees.
Plate beveling can be done manually by Houston skilled workers using handheld grinders.
Reasons for Beveling Metal Plates
Better Weld Penetration: One main reason to bevel plates is to allow better weld penetration when welding the plates together. The beveled edge creates an open groove that lets the welding electrode fully penetrate the joint between the two plates.
Without a beveled edge, it is very difficult for the weld to properly fuse and penetrate the joint's root. This leads to poor weld quality with cracks, porosity, and lack of fusion defects.
Proper bevel design based on the type of weld, plate thickness, and joint design allows the weld to be properly sized. This ensures full strength across the entire weld area.
Reduce Distortion
Thicker plates experience more distortion from the extreme heat of welding. Beveling reduces the total volume of weld metal required in the joint. Less weld metal means less heat input and distortion of the plates.
Using Houston plate beveling solutions, you can distribute the weld shrinkage more evenly over a larger area. This prevents excessive angular distortion at the joint area.
Improved Access
Beveled plates provide better access to the root of the weld joint compared to joining two squarely cut plate edges. The beveled groove makes it easier for the welder to position their electrode and properly fuse the joint root.
For tight joints in corners or confined spaces, a beveled opening may be the only way to get electrode access for root welding. Sufficient bevel angle ensures adequate workspace at the root area.
Fit-Up and Alignment
Having a beveled edge helps achieve tighter fit-up between plates being joined. Plates beveled to the proper angle can be more closely butted together at the root area.
On thicker plates, the bevels act as built-in alignment guides during plate fit-up. The matching beveled edges make it easier to properly align plates before welding.
Cost Savings
Though beveling adds preparation cost upfront, it actually saves money overall. By enabling proper weld quality and procedures, beveling prevents costly rework to repair defective welds.
Plate Beveling Solutions allow use of properly sized weld sizes based on bevels rather than over-sizing welds. Over-sized welds use excess weld metal and increase time/cost.
Better Quality Plate Welds
Bevel preparation on metal plates improves weld quality in several ways:
- Allows full weld penetration
- Reduces distortion and angular shrinkage
- Improves access for root welding
- Helps alignment and tight fit-up
- Enables use of proper weld sizing
- Prevents weld defects and need for repairs
For quality production welding of thick plate sections, beveling is an essential plate preparation step. Manual plate beveling solutions in Houston are critical in the metalworking industry.