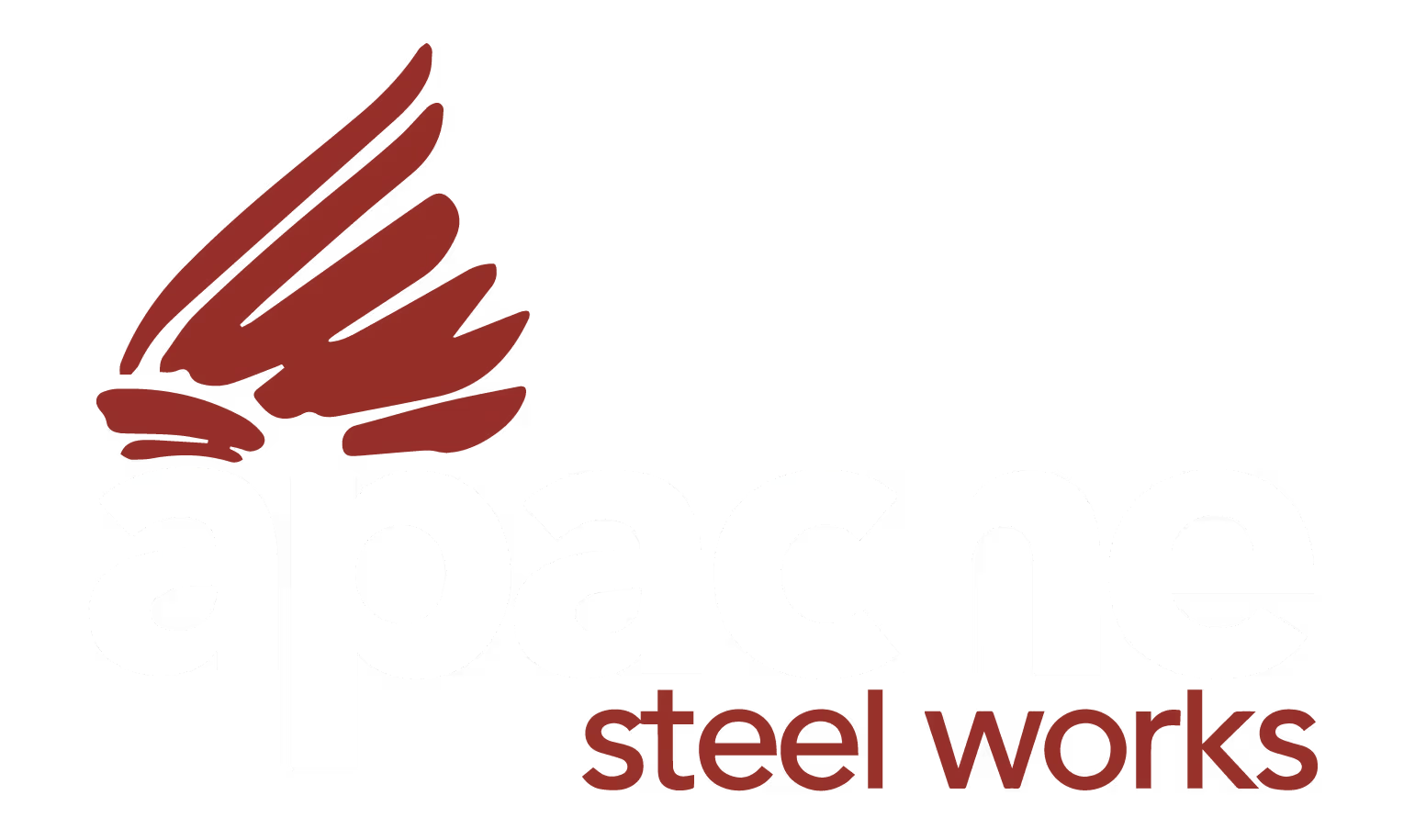
Plate Processing Company
When Is Sheet Metal Plate Beveling Needed?
When Is Sheet Metal Plate Beveling Needed?
Beveling is an important process in Houston sheet metal fabrication processes. It involves creating angled edges or chamfers on the plates that need to be welded together. Proper sheet metal plate beveling ensures strong, high-quality welded joints. But when exactly is this beveling required? Let's explore the key situations.
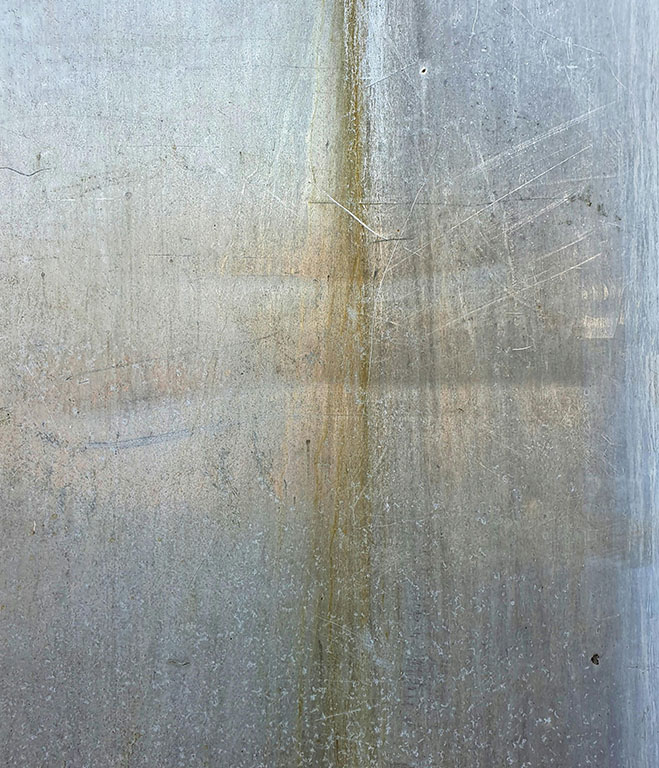
Thick Plate Welding
One of the most common cases where beveling becomes necessary is when welding thick plates or sections. As the metal thickness increases beyond a certain point, it becomes difficult to join the plates using just a simple square butt joint.
That's because for thick sections, the weld may not penetrate fully from one side. This can leave an un-welded root area, resulting in a weaker joint. Creating a bevel or groove joint geometry allows better access for the welding arc to properly fuse the joint root.
Common beveled joints for thick plate welding include single V, double V, U-groove and J-groove designs. The exact bevel angle and root face depend on factors like plate thickness, welding process and position.
Welding Codes and Procedures
There are welding codes and procedures that specify when beveling is mandatory based on the type of welded structure. For example, in pressure vessel fabrication following ASME codes, beveling is required for plates above certain wall thicknesses.
Similarly, in structural steel construction following AWS codes, Houston sheet metal plate beveling requirements kick in beyond specified material thicknesses. This ensures the welded joints meet the necessary strength and quality criteria for the application.
Even for thinner sheets, beveling may still be specified by certain critical codes and approved Welding Procedure Specifications (WPS) documents.
Fillet Weld Preparation
Sheet metal plate beveling finds application in creating better fillet weld profiles as well. When joining plates or sections at 90 degrees, a bevel or chamfer along the edges improves the accessibility and quality of the fillet welds.
The beveled edges allow the welder to better manipulate the torch/electrode and achieve proper fusion and wetting into the joint roots. This results in a stronger, higher integrity fillet compared to square edges.
Common bevel angles used for fillet weld preparation range from 30° to 45°, depending on the plate thickness, weld size and position.
Improving Weld Quality
In general, sheet metal plate beveling can enhance weld quality regardless of thickness. By creating an open root with better access, it enables:
- Complete joint penetration and fusion
- Proper tie-in at stop/start locations
- Easier removal of slag/contaminants
- Ability to execute stringer beads properly
This reduces issues like lack of penetration, entrapment of defects, poor bead profile and undercut - problems that can occur with square butt welds, especially on thicker sections.
Welding Special Materials
For welding materials that are thicker, harder or more crack-sensitive, sheet metal plate beveling becomes even more critical. These include:
- High strength alloy steels
- Stainless steels
- Nickel alloys
- Titanium alloys
The groove geometry from beveling provides better access for preheating, higher deposition rates and ease of removing defect-prone start/stop locations. It enables accommodating special welding techniques like butter layers that may be needed.
So in many ways, beveling improves the overall weldability and integrity when joining such special application materials.
Repairing Welds and Cutting Bevels
Apart from new welding, sheet metal plate beveling also has applications in repair and modification scenarios. When an existing weldment needs rectification or additions, cutting bevels on the areas to be reworked provides better access for welding.
So whether it is removing part of a defective weld, preparing for a pad or slice, or joining an extension - creating a beveled groove aids executing high-integrity repair welds.
Overall, the need for sheet metal plate beveling in Houston arises from metallurgical factors, application requirements, code specifications and basic welding principles. Appropriate beveling ensures strong, high-quality welds that meet the design and safety criteria across industries.