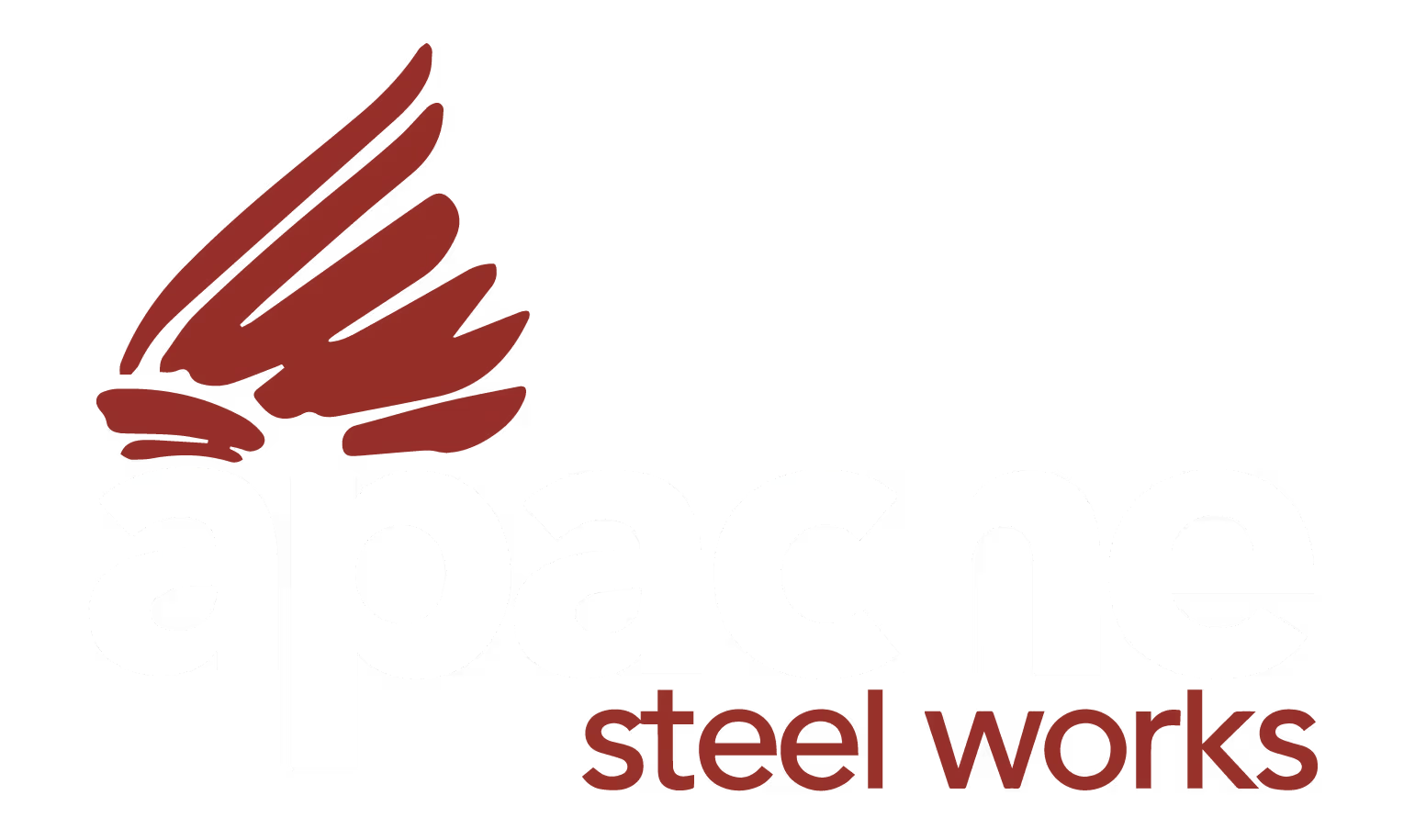
Plate Processing Company
What Is CNC Oxy Fuel Cutting and How Is It Used?
What Is CNC Oxy Fuel Cutting and How Is It Used?
CNC oxy-fuel cutting is a metalworking process that uses computer numerical control (CNC) along with fuel gases and oxygen to automatically cut through metals. While oxy-fuel cutting has been around for over 100 years, the integration of CNC technology has made it a highly automated and precise process that is still widely used today across many industries.
CNC oxy-fuel cutting is efficient and cost-effective and can handle various metal types and thicknesses with ease.
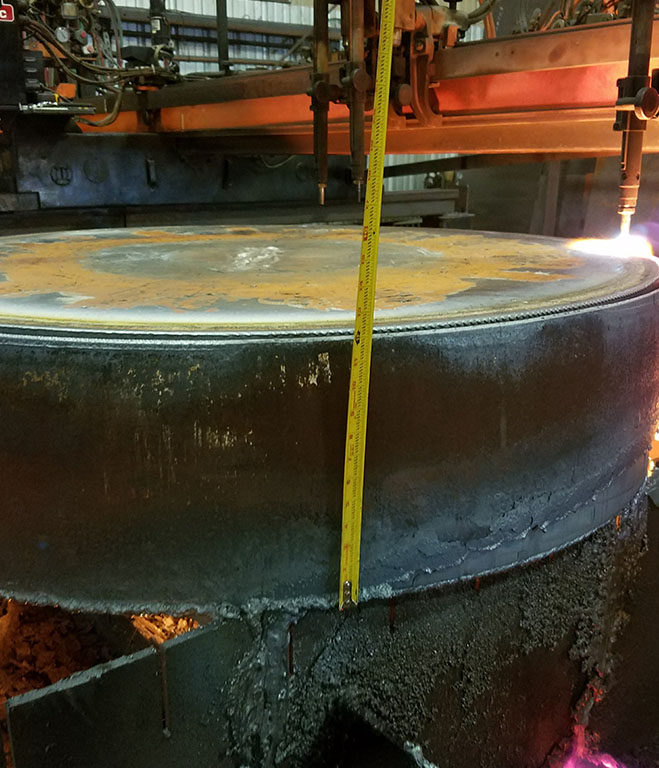
How Does CNC Oxy Fuel Cutting Work?
The cutting process occurs in three main steps controlled by the CNC machine - preheating, piercing, and cutting the metal material.
1. Preheating
First, the CNC cutting machine preheats the metal surface to extremely high temperatures, around 1800°F, using an intense flame. This preheat flame is created by mixing fuel gas like acetylene or propane with oxygen and igniting it at the CNC cutting torch tip.
The automated torch focuses the intense flame to heat a precise area of the metal to the required kindling temperature.
2. Piercing
Next, following the CNC program, a high-pressure stream of pure oxygen called the cutting oxygen is directed at this preheated spot. The oxygen causes rapid oxidation, chemically reacting with and melting the heated metal into a liquid slag.
As this automated cutting oxygen stream continues jetting through, it blows away the molten oxidized material, piercing a hole through the metal plate thickness.
3. Cutting the metal
Finally, the CNC machine moves the cutting torch along the programmed path while continuing to apply the preheating flame ahead to keep heating the metal to the kindling point. At the same time, the cutting oxygen stream maintains the melting, oxidation, and removal of metal slag.
This automated, uninterrupted process allows for highly accurate and consistent cut lines, angles or shapes to be made efficiently through the metal workpiece.
Versatile CNC Applications
Manufacturing
CNC oxy fuel proficiently cuts complex contoured shapes, holes, and intricate patterns in metal parts for manufacturing vehicles, machinery, molds, and more. Automated precision fabrication increases productivity.
Heavy Fabrication
Its ability to precisely cut through an extremely thick plate and sectional metal is valuable for industries like shipbuilding, offshore structures, mining equipment fabrication, and other major projects. CNC oxy fuel remains crucial for these heavy-duty cutting needs.
Demolition and Salvage
This CNC-controlled cutting technique helps in demolishing and salvaging operations by automatically cutting and separating huge metal structures like machinery, vessels, or equipment into manageable pieces for recycling or disposal.
Metalworking and Repair
At workshops and sites, CNC oxy fuel accurately bevels, cuts, and prepares metal surfaces/edges for subsequent welding, joining, or repair processes to be seamlessly performed.
Although oxy fuel cutting is an established process, the incorporation of CNC technology has enhanced its automation, accuracy, and productivity for various materials and thicknesses. Its versatility, combined with efficiency and precision, makes CNC oxy fuel cutting essential for manufacturing, heavy fabrication, demolition, and metalworking operations today.