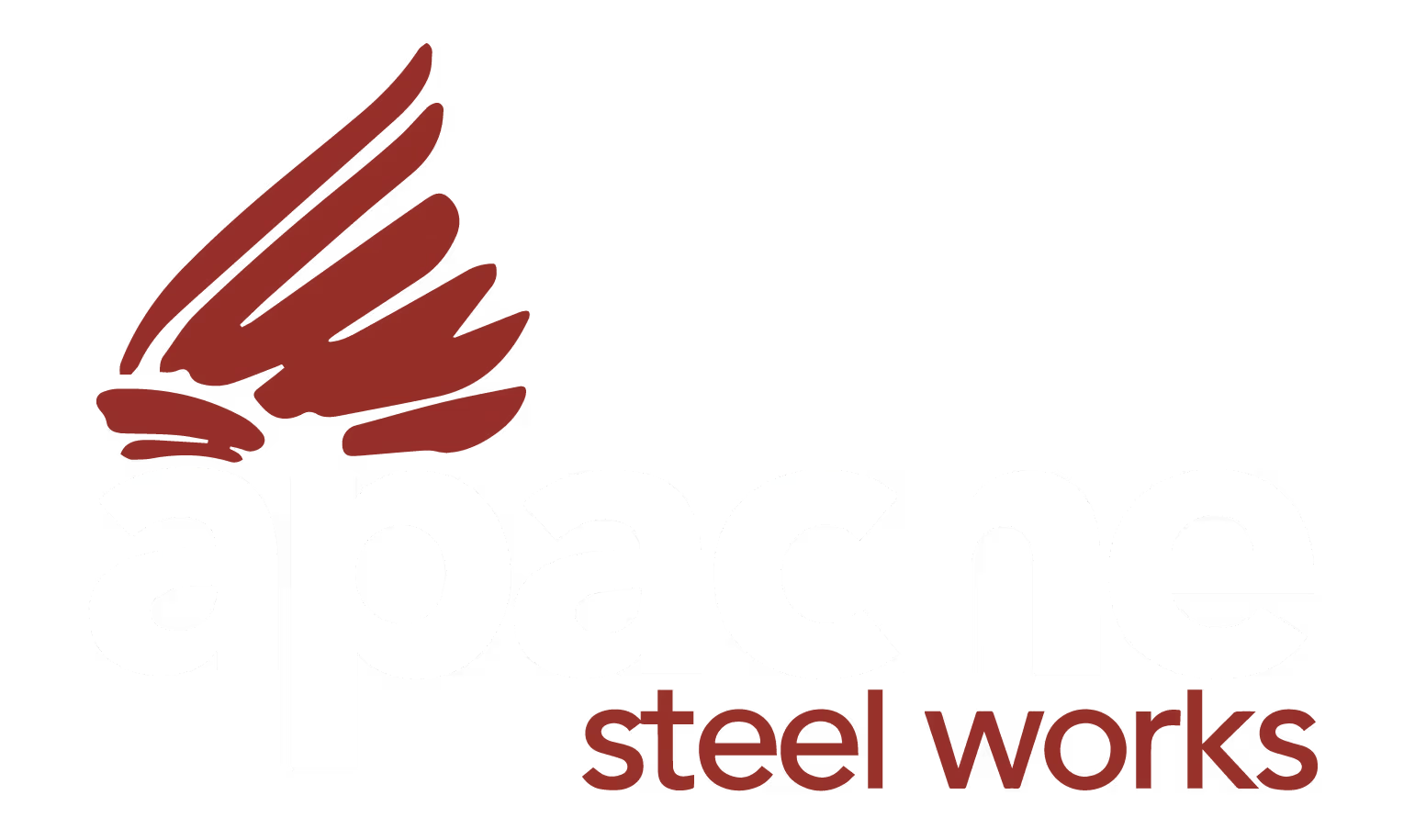
Plate Processing Company
What does a sheet metal plate forming and rolling process involve?
What does a sheet metal plate forming and rolling process involve?
Metal shapes our modern buildings, vehicles, and machinery through careful forming and rolling processes. Sheet metal plate forming and rolling in Houston helps transform flat metal sheets into curved, bent, and shaped products that serve various industrial needs. This guide explores the detailed steps and methods used to shape metal plates into useful products.
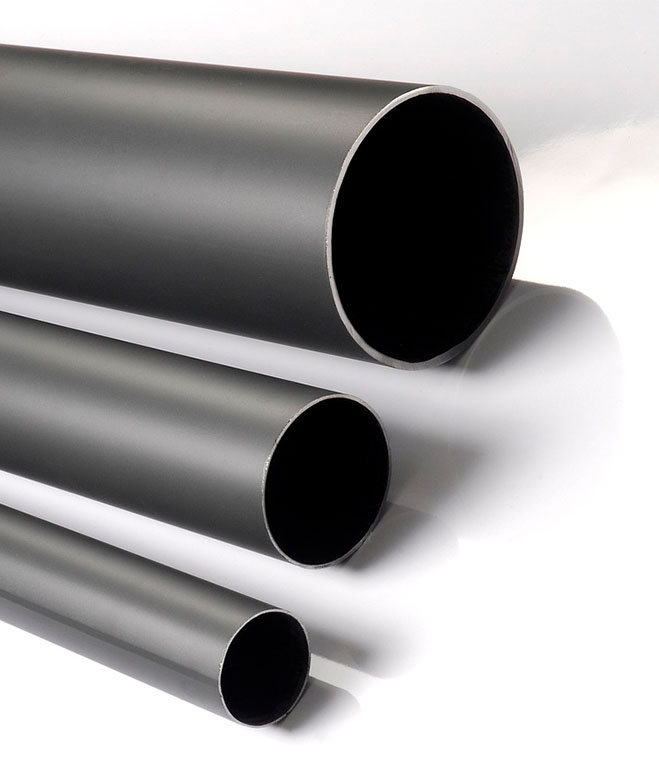
The Basic Process Steps
Sheet metal plate forming and rolling in Houston starts with careful planning and preparation. First, technicians measure and mark the metal sheets according to design specifications. They check the metal thickness, grade, and quality to ensure it matches project requirements. The metal surface undergoes cleaning to remove any dirt, oil, or oxidation that could affect the forming process.
Before any actual forming begins, operators calculate important factors like:
- Bend allowances
- Spring-back compensation
- Minimum bend radius
- Material stretch factors
- Required pressure settings
Professional sheet metal plate forming and rolling in Houston services use these calculations to program their machines and set up the proper tooling. This preparation helps prevent common problems like over-bending, material cracking, or uneven curves.
Types of Forming and Rolling Operations
Sheet metal plate forming and rolling in Houston includes several main processes that shape metal in different ways. Each method serves specific purposes and creates different shapes:
Plate Rolling
The rolling process changes flat metal plates into curved or cylindrical shapes. Large rollers apply steady pressure to gradually bend the metal. This process can create:
- Large storage tanks
- Industrial pipes
- Architectural columns
- Curved panels
- Structural supports
The metal passes through the rollers multiple times, with each pass increasing the curve until reaching the desired shape. Skilled operators adjust roller spacing and pressure to control the final diameter and prevent flat spots or kinks.
Press Brake Forming
Press brake forming creates precise bends in metal plates. This process uses:
- Different die shapes
- Various bend angles
- Multiple bend sequences
- Precise pressure control
- Special edge treatments
Operators must carefully position the metal and control the press brake to create accurate bends. Sheet metal plate forming and rolling in Houston facilities often use computer-controlled press brakes for consistent results across multiple pieces.
Quality Control and Testing during Sheet Metal Plate Forming and Rolling
Quality checks happen throughout the forming process to ensure accuracy. Technicians measure:
- Bend angles using special gauges
- Cylinder roundness with templates
- Surface finish quality
- Overall dimensions
- Material integrity
They also check for common problems like:
- Material cracking
- Uneven curves
- Surface marks
- Incorrect angles
- Edge deformation
Each piece undergoes inspection before moving to the next production stage. This careful checking helps maintain high quality standards and prevents costly mistakes.
Material Handling and Safety
Proper handling keeps both workers and materials safe during forming operations. Sheet metal plate forming and rolling in Houston facilities follow strict safety procedures including:
Material Movement
- Using proper lifting equipment
- Following safe stacking methods
- Protecting metal surfaces
- Maintaining clean work areas
- Using appropriate storage racks
Worker Safety
Workers must use:
- Heavy-duty gloves
- Steel-toed boots
- Eye protection
- Back support when needed
- Proper lifting techniques
These safety measures prevent injuries and protect the metal from damage during forming operations.
Common Applications of Sheet Metal Plate Forming and Rolling
The forming and rolling process creates many different products used in various industries. Common applications include:
Industrial Uses
- Storage tanks and vessels
- Large diameter pipes
- Structural supports
- Machine housings
- Industrial ductwork
Construction Applications
- Curved roof panels
- Architectural features
- Building columns
- Decorative elements
- Support structures
Each application requires specific forming techniques and quality standards to ensure the final product meets its intended use.
Understanding these processes helps customers work better with sheet metal plate forming and rolling companies in Houston. Whether needing simple bends or complex curved shapes, knowing the basics of metal forming helps communicate requirements clearly and ensure satisfactory results. The right forming technique, combined with proper quality control, creates durable and accurate metal products that serve their intended purpose well.