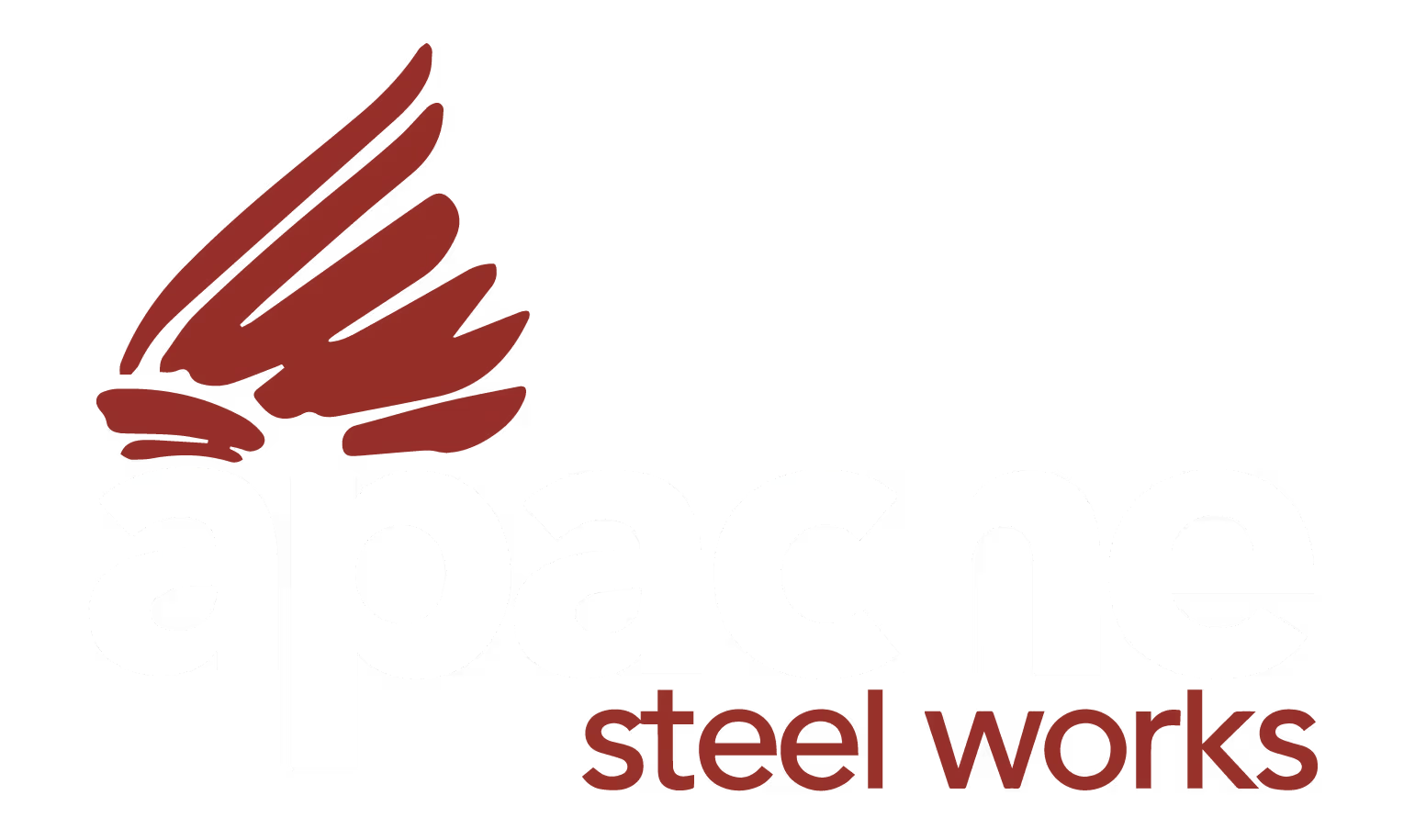
Plate Processing Company
The Role of Flame Cutting in Heavy Equipment Manufacturing
The Role of Flame Cutting in Heavy Equipment Manufacturing
Precision and efficiency are essential in the manufacturing of heavy equipment. Fabricating large steel components demands advanced cutting technologies to meet tight tolerances and production deadlines. For companies in Houston and the surrounding region, flame cutting services play a crucial role.
Two common methods used for steel flame cutting in Houston are CNC plasma and oxy-fuel steel plate cutting. But what exactly are these processes, and how do they contribute to heavy equipment manufacturing? Let's take a closer look.
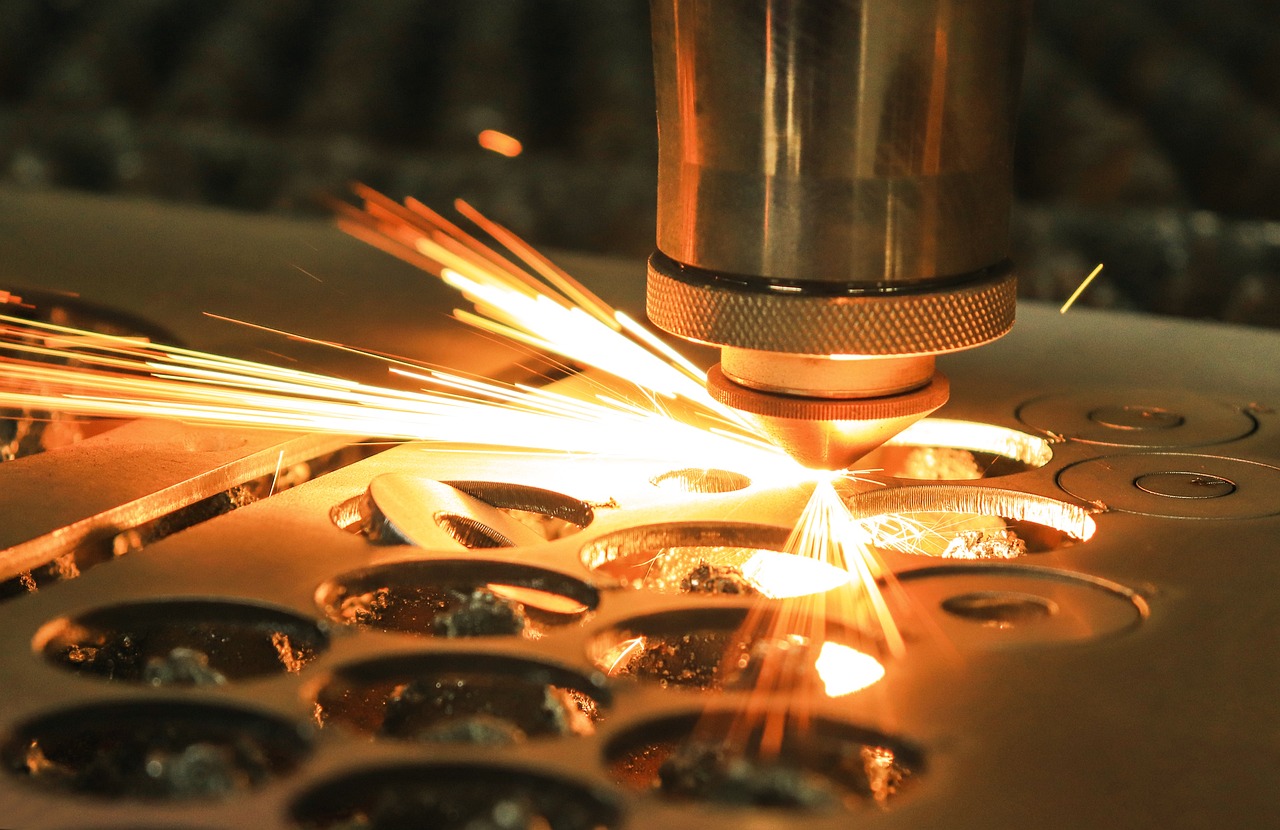
CNC Plasma Cutting
CNC (computer numerical control) plasma cutting uses a precision, high-energy plasma arc to cut through steel plates and fabricated metal. With the torch connected to a CNC machine, it can accurately follow programmed toolpaths to produce intricate cuts, beveled edges, holes, and profiling on flat steel plate stock.
The Key Advantages of CNC Plasma Include:
Speed - Plasma is over three times faster than conventional cutting, maximizing productivity and throughput. Manual rework is also reduced by digital precision.
Versatility - From structural steel plates to decorative cladding, plasma can cut all conductive metals with superior edge quality. It handles thicknesses from gauge to over 2” inch.
Cost-Efficiency - Low operating costs, consumable longevity, and minimized scrap make plasma the smart choice.
Houston's heavy equipment industry demands plasma's accuracy and efficiency for steel flame cutting in Houston because of components like truck frames, components for excavators, and agricultural machinery. With part nesting and automation, fabrication shops leverage CNC plasma to optimize workflows.
Oxy-Fuel Cutting
Alternatively, oxy-fuel (or oxy-acetylene) cutting uses a precise mixture of oxygen and pressurized fuel gas to preheat steel to over 2,000°F and then cuts by rapidly oxidizing the metal. While not as fast as plasma in thinner materials, oxy-fuel provides superior versatility in thick plate applications.
Key Advantages of Oxy-Fuel Include
Thick Cutting - Oxy-fuel is ideal for cuts over 1" thick, even up to 14" steel plate or more. Superior penetration for thick materials.
Versatility - Oxy-fuel can cut virtually any metal, from steel to cast-iron. Preheating also enables cutting underwater or removing frozen pins.
The ability to cut through the thickest steel plate with quality, clean edges makes oxy-fuel indispensable in heavy fabrication.
Maximizing Productivity
Whether manufacturing new off-road haulers in Houston's industrial corridor or producing replacement parts, local heavy equipment companies value expertise, quality, and quick turnaround times. With state-of-the-art CNC plasma and oxy-fuel cutting, along with a portfolio of complementary technologies, Houston's flame cutting pros deliver on every project.
Therefore, flame cutting remains an indispensable process in the production of heavy equipment across various industries in Houston's manufacturing sector. For efficient steel processing and plate fabrication, partner with an experienced provider for steel plate cutting in Houston.