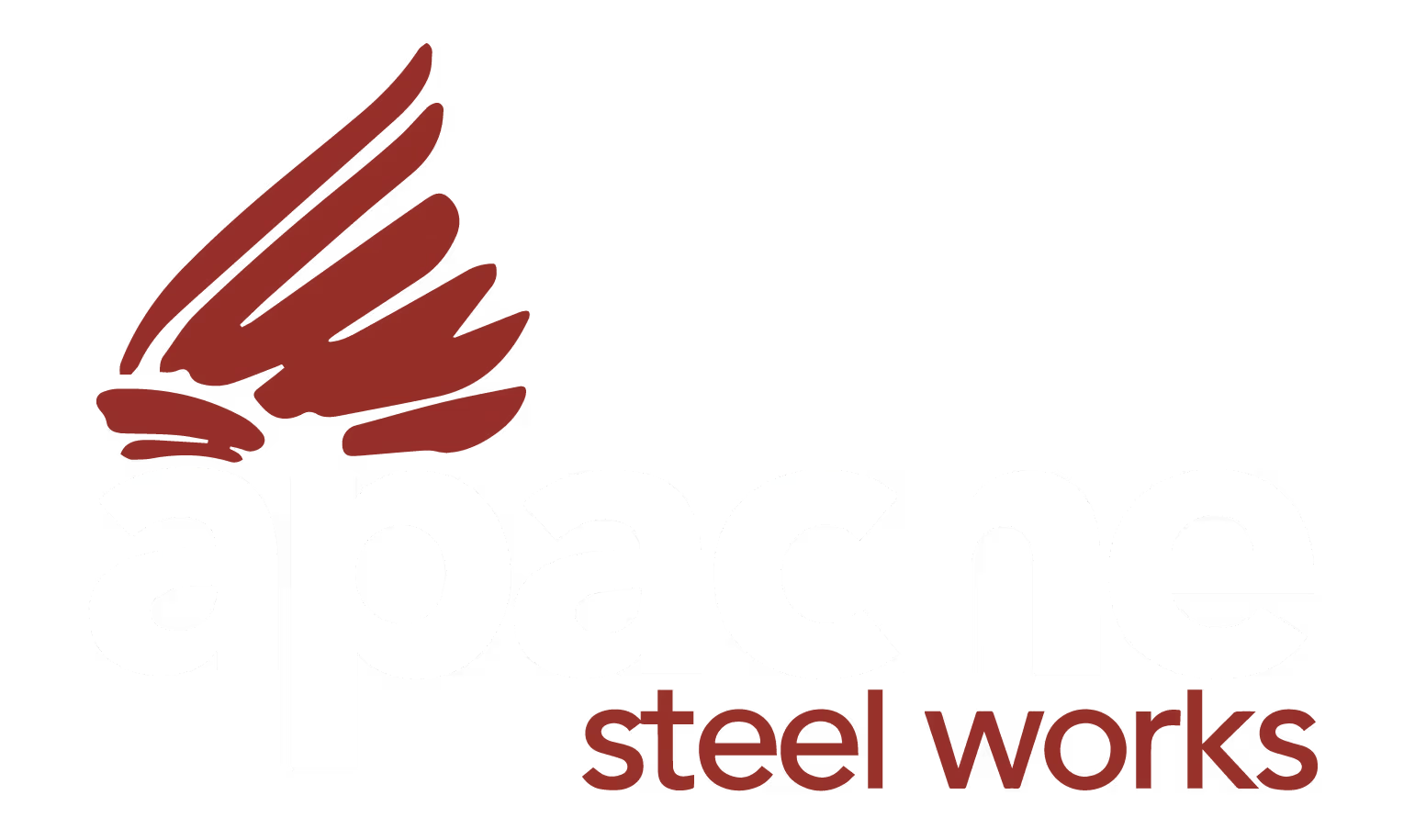
Plate Processing Company
The Impact of Sheet Metal Plate Beveling on Welding Quality
The Impact of Sheet Metal Plate Beveling on Welding Quality
Sheet metal plate beveling emerges as a silent hero in welding preparation in the heart of Houston's industrial fabric, where precision and excellence are non-negotiable. Sheet metal plate beveling in Houston is critical to ensuring strong, reliable welds and maintaining the highest standards across diverse industries in Houston.
Let us examine how, in Houston's ever-changing industrial landscape, this seemingly straightforward process enhances welding outcomes.
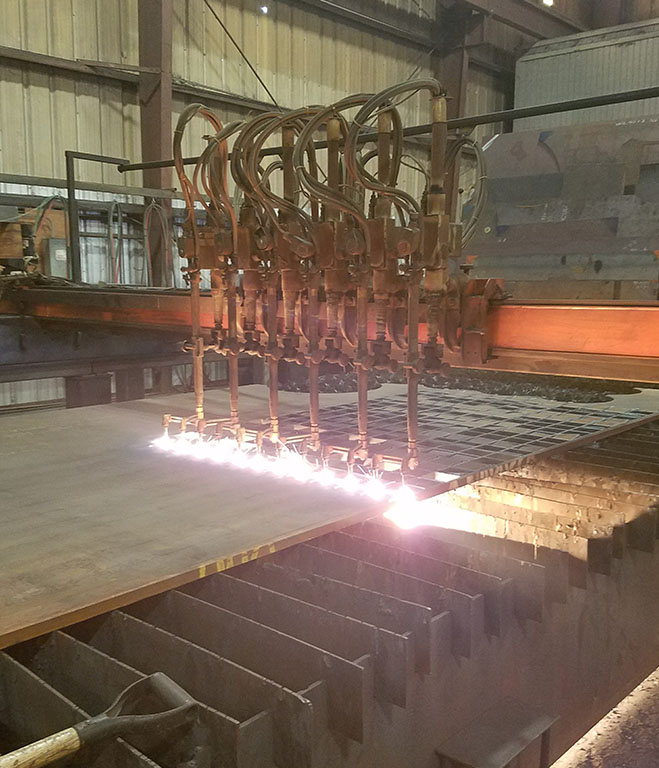
Why Beveling Is Important
Excellence in welding is based on a strong foundation of weld preparation. Sheet metal plate beveling is the removal of material from the edges of metal plates to create a groove or bevel that allows the weld to penetrate properly. For several reasons, the beveling process is critical:
- Better Weld Penetration
- Improved Weld Quality
- Reducing Welding Defects
How Beveling Improves Welding Precision: A Step-by-Step Guide
Welding Preparation
The initial step in the beveling process involves carefully preparing metal plates before welding. This entails removing a certain amount of material from the edges, resulting in a groove or bevel. The welding parameters, which include elements such as material thickness and the welding procedure to be used, define the depth and angle of the bevel.
Maintaining Consistent Bevel Angles
Sheet metal plate beveling in Houston ensures that the prescribed bevel angles are maintained consistently over the whole length of the connection, which is critical in welding. This uniformity is crucial for establishing consistent heat distribution throughout the welding process, which contributes to the weld's overall stability and strength.
Heat-Affected Zone Reduction
Excessive heat during welding can cause unwanted changes in the characteristics of the material, resulting in weaker welds. Proper beveling is critical to reducing heat-affected zones (HAZ). Beveling enables more effective heat dissipation during welding by creating a well-prepared groove, which maintains the structural integrity of the metal surrounding the weld joint.
Improving Welder Accessibility
The beveled groove facilitates better access to the welding flame or electrode in addition to serving as a welding process guide. When the junction is easily accessible due to the beveled edges, welders can navigate and oversee the welding process more effectively. This improved accessibility contributes to the overall welding process's accuracy and efficiency.
Selecting the Correct Bevel Type
The choice of bevel type is critical and is determined by the welding needs and material properties. V, X, Y, and K bevels are common bevel types, each suited to unique welding tasks. The proper bevel type guarantees that the weld joint is effectively prepared for the welding process, which contributes to the overall success of the weld.
Increasing Weld Penetration
Improved weld penetration is one of the key goals of beveling. A suitably beveled edge helps the welding arc or filler material penetrate deep into the joint, resulting in a strong fusion of the neighboring metal plates. This deep penetration adds to the weld's overall strength and endurance, making it resistant to external pressures.
The step-by-step method of sheet metal plate bevelingin Houston is critical to improving welding proficiency. The efficiency of welding operations in Houston is improved at every stage of the beveling process, from precise preparation and maintaining constant angles to minimizing heat-affected zones and increasing weld penetration.