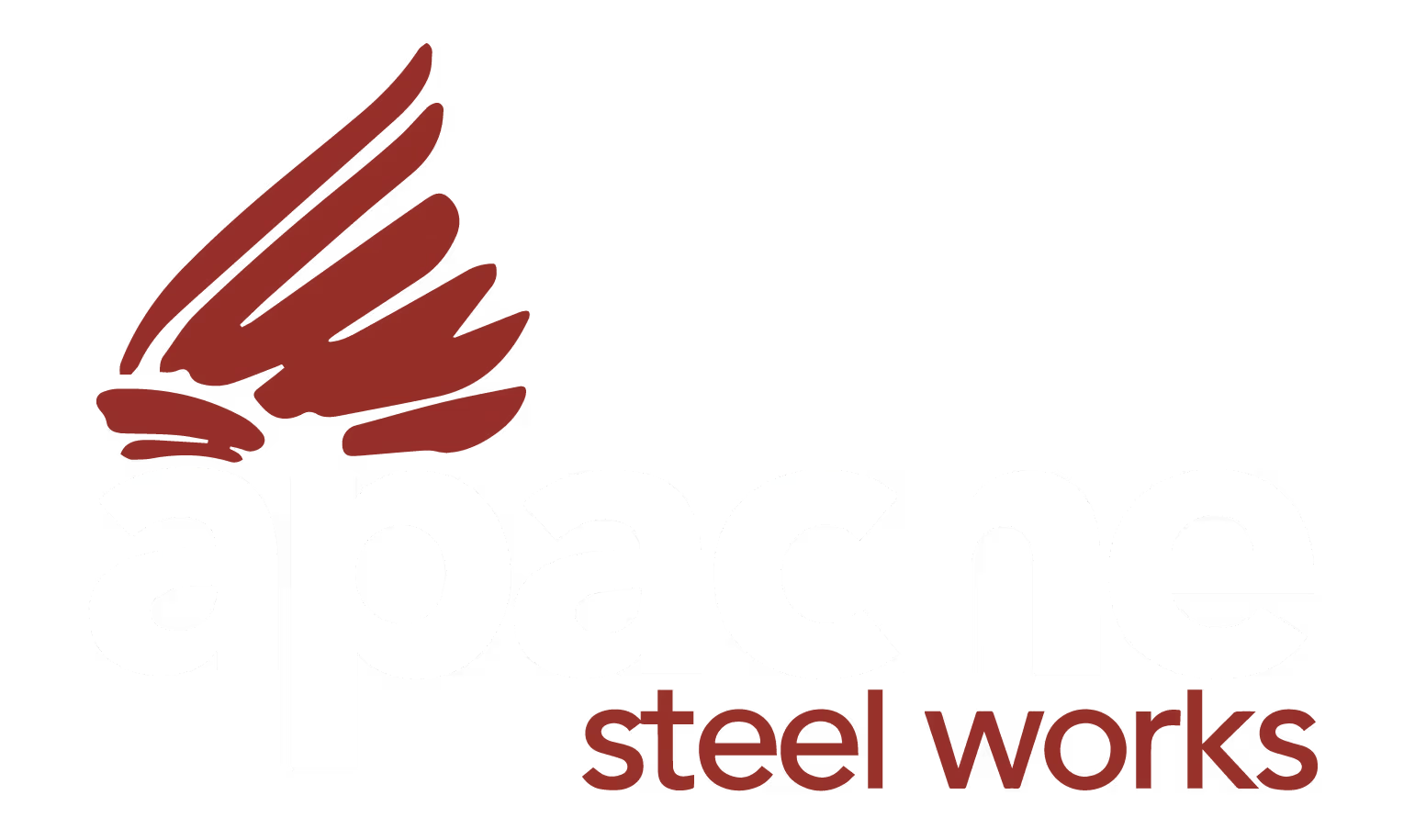
Plate Processing Company
Oxi Fuel Cutting in Houston: Maximizing Manufacturing Precision and Efficiency
Oxi Fuel Cutting in Houston: Maximizing Manufacturing Precision and Efficiency
Metal fabrication demands precise and cost-effective cutting technologies, and oxi fuel cutting emerges as a reliable solution for industries seeking exceptional material processing capabilities. This specialized technique combines oxygen and fuel gases to create a powerful cutting method that transforms industrial manufacturing approaches.
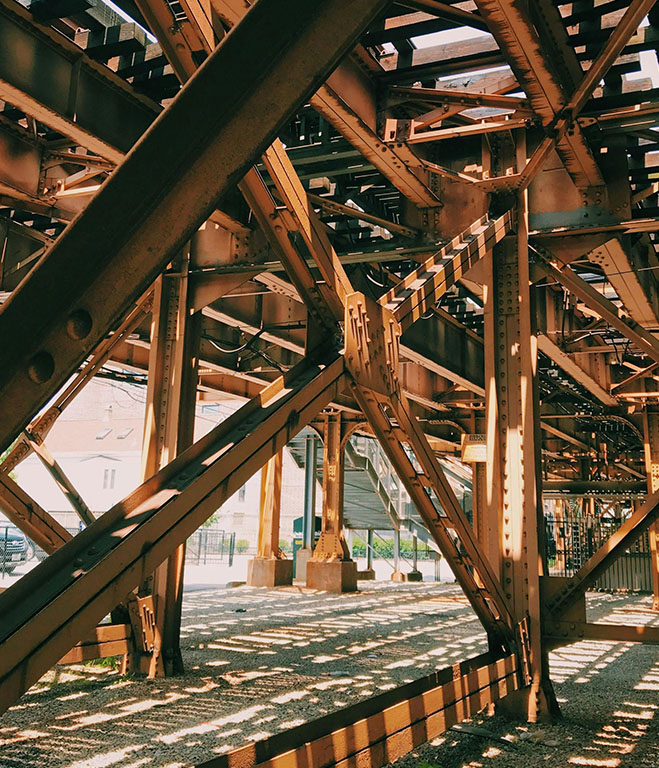
Understanding Oxi Fuel Cutting Fundamentals
Oxi fuel cutting represents a sophisticated thermal cutting process that generates extreme temperatures to slice through metal materials. The technique involves combining pure oxygen with combustible fuel gases like acetylene, creating a high-temperature flame capable of melting and separating metal surfaces with remarkable precision. Oxi fuel cutting in Houston has become a cornerstone technology for manufacturers seeking efficient and economical metal processing solutions.
Technical Mechanism of Oxi Fuel Cutting
The cutting process initiates by preheating metal surfaces to their ignition temperature using a precisely controlled flame. Once the material reaches the critical temperature, a high-pressure oxygen stream is introduced, causing rapid oxidation and metal removal. This chemical reaction enables clean and precise cuts across various metal thicknesses and compositions.
Material Compatibility and Performance Characteristics
Oxi fuel cutting demonstrates exceptional versatility in processing ferrous metals, particularly carbon steel. The technique works effectively on metal plates ranging from thin sheets to substantial industrial-grade materials. Manufacturers utilizing oxi fuel cutting in Houston appreciate its ability to handle diverse material specifications with consistent performance and minimal waste.
Economic Advantages and Cost Considerations
Compared to alternative cutting technologies, oxi fuel cutting offers significant economic benefits. The process requires minimal initial equipment investment and demonstrates low operational costs. Manufacturers can achieve substantial cost savings through reduced material waste, faster cutting speeds, and decreased secondary processing requirements.
Equipment and Technical Specifications
Professional oxi fuel cutting systems incorporate sophisticated components designed for precision and reliability. These include specialized torch assemblies, precise gas flow regulators, advanced flame control mechanisms, and robust mechanical frameworks. Carefully calibrated equipment ensures consistent cutting performance across different industrial applications.
Safety and Operational Protocols
Implementing oxi fuel cutting requires comprehensive safety measures and specialized operator training. Professionals must wear appropriate personal protective equipment, including flame-resistant clothing, protective eyewear, and heat-resistant gloves. Proper ventilation, fire prevention strategies, and rigorous equipment maintenance are crucial for safe and effective operations.
Industrial Applications and Versatility
Oxi fuel cutting finds extensive applications across multiple industrial sectors, including metal fabrication, construction, shipbuilding, and automotive manufacturing. The technique's adaptability makes it suitable for creating structural components, industrial machinery parts, and specialized metal assemblies.
Precision and Cut Quality Considerations
Cutting quality depends on multiple factors such as flame temperature, oxygen pressure, torch design, and operator expertise. Modern oxi fuel cutting systems enable manufacturers to achieve precise cuts with minimal material distortion and exceptional edge quality. Skilled operators can execute complex geometrical designs and intricate metal processing requirements.
Maintenance and Performance Optimization
Regular equipment maintenance ensures consistent oxi fuel cutting performance. This involves periodic torch calibration, gas system inspection, and comprehensive equipment cleaning. Proper maintenance helps prevent performance degradation and extends the operational lifespan of cutting equipment.
Environmental and Operational Efficiency
Oxi fuel cutting offers notable environmental advantages compared to alternative thermal cutting methods. The process generates minimal hazardous waste, consumes less energy, and produces cleaner cutting outcomes. Manufacturers can achieve sustainable metal processing while maintaining high productivity standards.
The landscape of industrial metal fabrication continues to evolve, with oxi fuel cutting representing a critical technology for manufacturers seeking precision, efficiency, and economic performance. By understanding its technical nuances and operational advantages, industries can leverage this powerful cutting solution to achieve exceptional manufacturing outcomes.