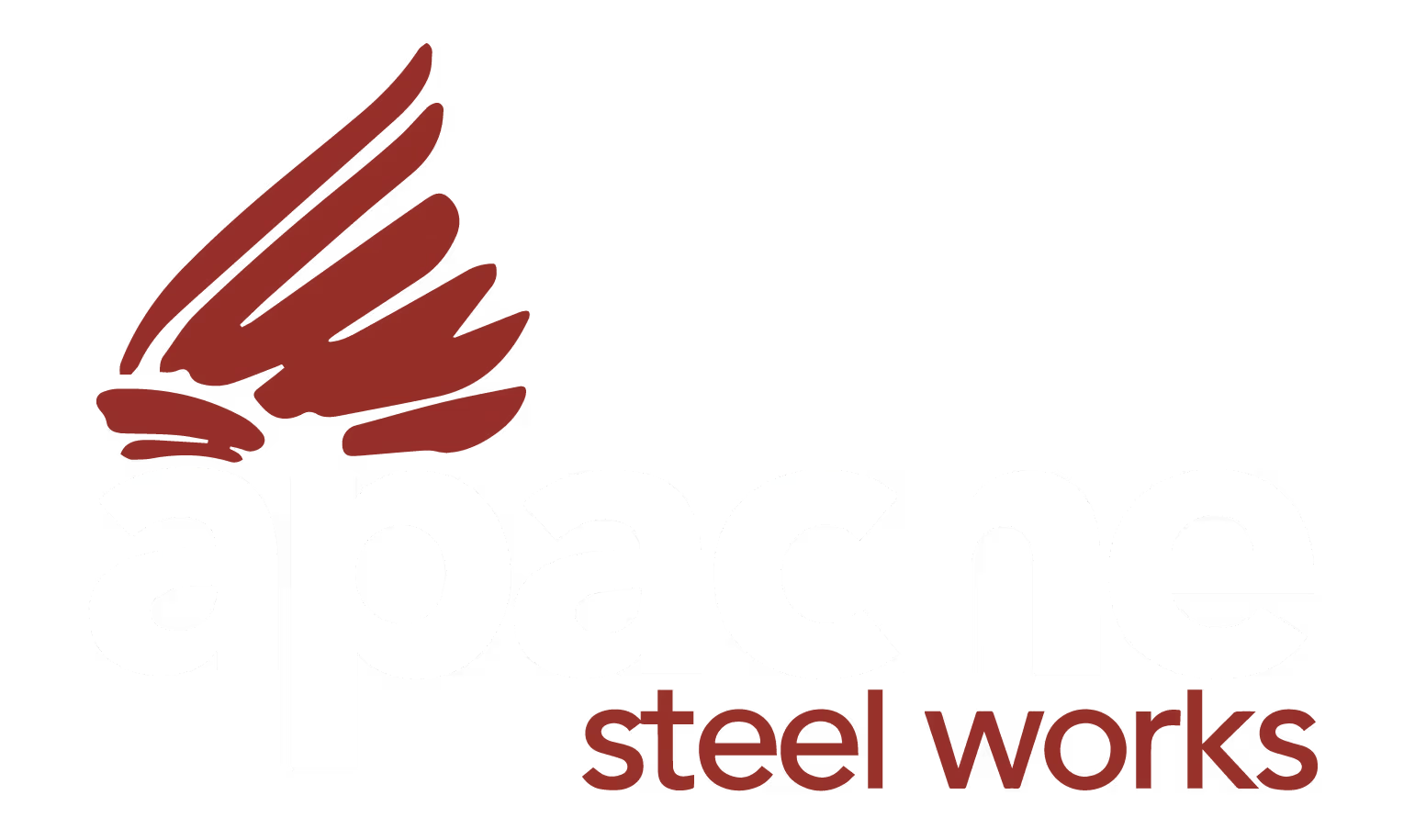
Plate Processing Company
Manual Plate Beveling: Why Is It Still in Trend?
Manual Plate Beveling: Why Is It Still in Trend?
Plate beveling is the process of creating angled edges on metal plates. These beveled edges allow for better weld penetration and stronger joints when joining plates together. While modern CNC machining provides automated beveling, manual plate beveling in Houston remains a popular choice in many situations.
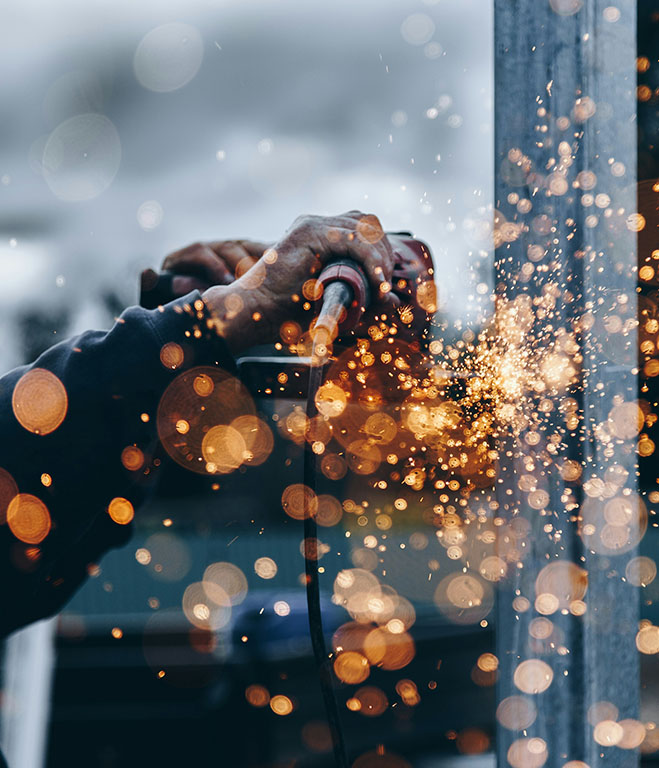
What Is Manual Plate Beveling?
In manual plate beveling, a worker uses a handheld power tool to cut the required bevel angle onto the plate edges. Common tools include:
- Portable beveling machines
- Angle grinders fitted with special beveling discs or wheels
- Oxy-fuel beveling torches
The worker guides and controls the beveling tool along the plate's edge to create the desired angled cut or chamfer. Proper safety gear like gloves, masks and protective clothing is required.
Advantages of Manual Plate Beveling
Despite the availability of automated CNC beveling machines, manual methods continue to be widely used due to certain key advantages:
Versatility: Manual plate beveling in Houston can be done on plates of any size, shape or thickness easily. Automated machines have size limitations.
Accessibility: Handheld tools allow beveling at the worksite itself, like construction sites or on large fabrications.
Cost-Effective: Basic beveling tools are inexpensive compared to entire CNC systems. This suits small job volumes.
Skill Development: Manual beveling helps develop valuable hands-on skills in workers, promoting craftsmanship.
Another advantage of manual plate beveling in Houston is the ability to create custom bevels on an as-needed basis. For example, if a particular weld joint design requires a unique bevel geometry, a skilled beveler in Houston can precisely cut that profile using their tools and techniques. This kind of customization is difficult with pre-programmed CNC beveling machines.
Moreover, manual beveling promotes a hands-on understanding of how bevels affect weld quality. Experienced bevelers can adjust the bevel angle, root face, and other parameters based on the specific welding process, materials, and joint design. This intuitive knowledge gained through manual work helps ensure optimal weld performance.
Finally, in certain harsh environments like offshore platforms or mining sites, the portability and ruggedness of manual beveling tools make them better suited compared to sophisticated CNC systems. The simple and self-contained nature of the manual methods is an advantage in such challenging work conditions.
When Is Manual Beveling Preferred?
There are several common scenarios where the manual beveling approach makes more sense:
Small Job Lots: For small numbers of plates or one-off jobs, setting up automated equipment is not economical.
Varying Plate Sizes: When plate dimensions constantly vary, manual methods provide more flexibility.
On-Site Work: Beveling plates at remote construction sites is easier with portable manual tools.
Repair Work: Manual beveling facilitates altering existing weldments during repair or modification work.
Training: It is used for training welders and fitters in proper beveling techniques.
Certain Industries: Industries like shipbuilding still rely heavily on manual plate beveling skills.
Types of Manual Bevels
Depending on the application and joint design, different bevel profiles may be required such as:
- Single V-bevel
- Double V-bevel
- J-bevel
- U-groove
- Compound bevels
Highly skilled bevelers can create these profiles precisely using just their handheld tools and guides.
Safety Precautions
While convenient, manual beveling poses some safety risks that require precautions. Proper training, personal protective equipment and workplace safety practices are essential.
The Future of Manual Beveling
Despite the growth of automated CNC beveling technology, manual plate beveling skills remain highly relevant in Houston. Many large projects still rely on these traditional methods.
As long as welding continues to be an integral part of metal fabrication and construction, the demand for skilled manual bevelers will likely continue. The trends point towards manual beveling complementing rather than being fully replaced by automation.