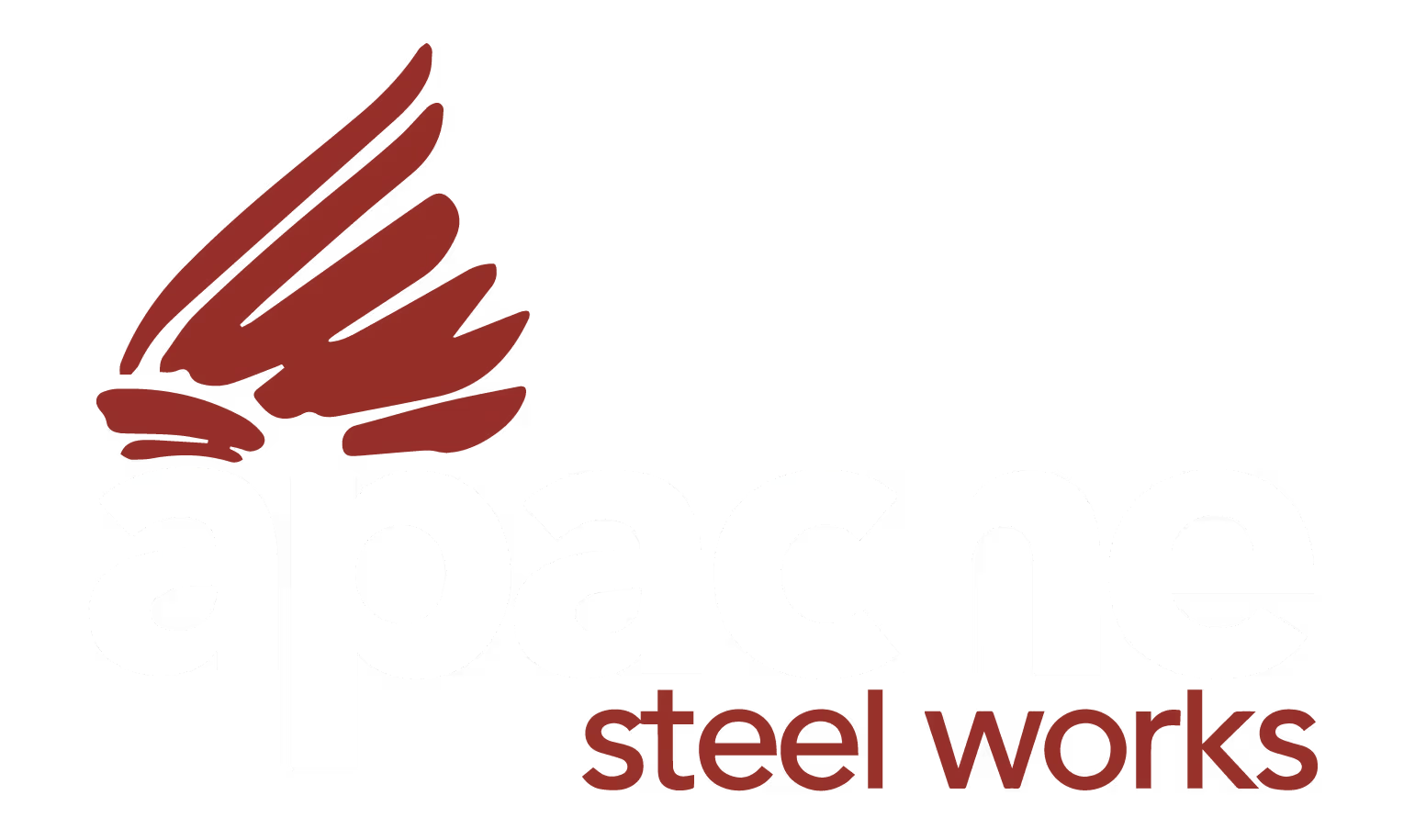
Plate Processing Company
HD Plasma Cutting vs. Laser Cutting: Which Is Best for Your Houston Project?
HD Plasma Cutting vs. Laser Cutting: Which Is Best for Your Houston Project?
When it comes to industrial metal cutting, two of the most widely used methods in Houston are HD plasma cutting and laser cutting. However, the superiority of HD plasma cutting over laser cutting becomes evident when considering most industrial and fabrication applications. This blog will break down the distinctions between plasma cutting and laser cutting so you can choose which method is better for your Houston project.
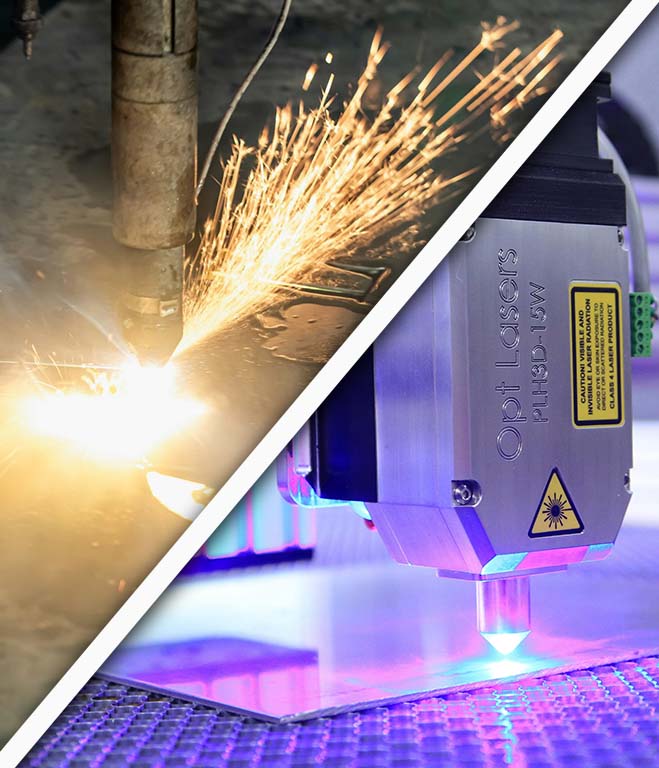
Understanding HD Plasma Cutting
What is HD Plasma Cutting?
HD plasma cutting stands as an enhanced version of standard plasma cutting where a directed plasma jet achieves quick slicing of conductive materials at high speed. The process involves:
- The electric arc formation links the electrode to the workpiece material for gas ionization.
- Energy-dense plasma blasting functions to melt and eject away the metal material.
- The use of a special nozzle system provides better cut quality along with decreased bevel angles.
Limitations of HD Plasma Cutting
HD Plasma cutting leads to better results but it also presents some small performance limitations.
- The kerf width produced by plasma machines slightly surpasses laser widths though this difference proves insignificant for most industrial purposes.
- The HAZ becomes larger than laser cutting HAZ however appropriate settings and cooling measures reduce this issue.
Understanding Laser Cutting
What is Laser Cutting?
Laser cutting operates with a focused laser beam that has enough power to produce heat that melts or vaporizes the steel material. Laser cutting serves applications which need precision like electronics and fine-detail engraving.
Limitations of Laser Cutting
1. Very Expensive
- The price of a high-powered fiber laser system exceeds the cost of an HD plasma system by 5 to 10 times.
- The required maintenance expenses grow at an exponential rate because of optical systems as well as the need for gasses and cooling mechanisms.
2. Slow on Thick Materials
- Between 1/4 inch and thicker material thicknesses the laser cutting process becomes gradually slower.
- A thick material needs several consecutive laser passes that lengthens total production time.
3. Limited Material Compatibility
- Special hardware and high prices become necessary for efficient processing of aluminum brass and copper and other reflective metals through laser cutting.
- Surface contaminants have greater negative impact on this cutting method than plasma cutting does.
Which Cutting Method is Right for Your Project?
When to Choose HD Plasma Cutting
- If you need fast cutting speeds on medium-to-thick materials.
- If you’re cutting steel, aluminum, or other conductive metals efficiently.
- If cost is a factor then plasma cutting offers the best balance of affordability and performance.
- If your material has coatings, rust, or imperfections that would interfere with laser cutting.
When to Choose Laser Cutting
- If your application requires ultra-fine detail and minimal finishing work.
- If you primarily cut thin sheet metal (under 1/4 inch).
- If cost is not a concern, and you need highly automated precision cutting.
Conclusion
Industrial fabrication and most industrial applications benefit optimally from HD plasma cutting over laser cutting. The technology offers unmatched quick performance combined with affordability as well as wide applicability for cutting metals of greater thickness. For most cutting needs, HD plasma cutting in Houston stands as the better option and precision on small sheet metal is the only condition where laser cutting becomes superior.