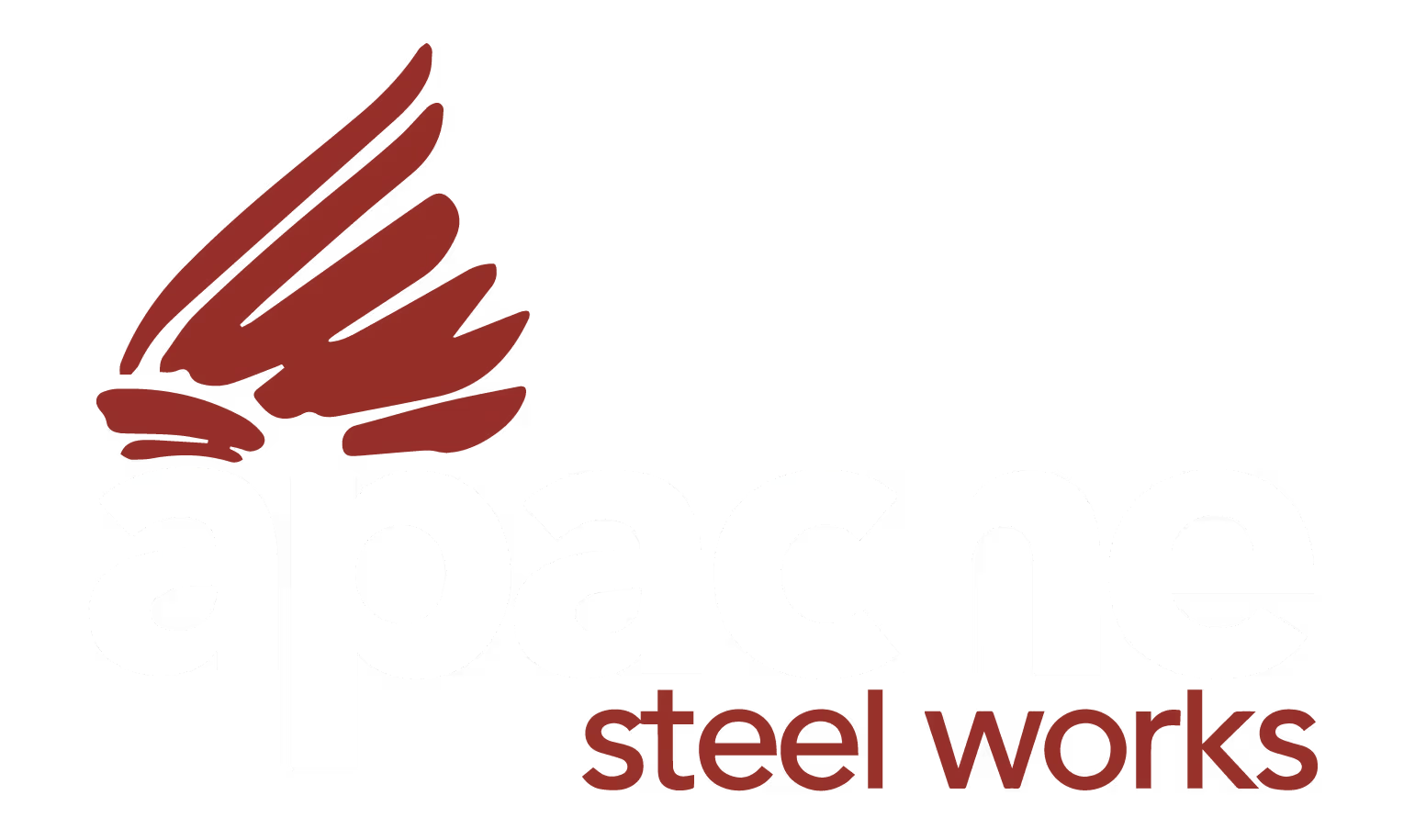
Plate Processing Company
HD Plasma Cutting vs. Conventional Plasma Cutting: A Comparative Guide
HD Plasma Cutting vs. Conventional Plasma Cutting: A Comparative Guide
Metal fabrication technologies have witnessed significant advancements, particularly in plasma cutting methods. HD plasma cutting in Houston represents a notable enhancement over conventional plasma cutting techniques, offering distinct advantages in precision and efficiency. This analysis examines the critical differences between these two cutting technologies.
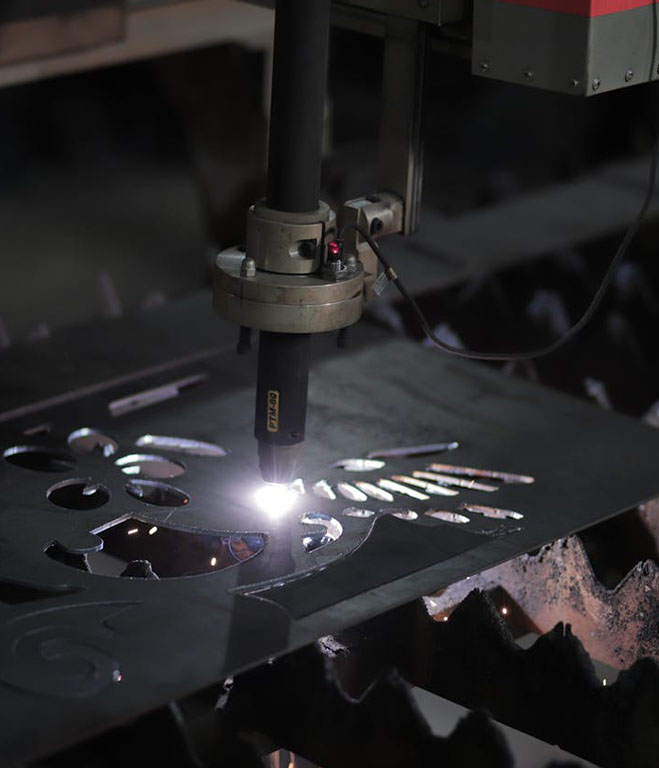
Fundamental Technology Differences
HD plasma cutting employs sophisticated gas injection and arc focusing technologies that distinguish it from conventional methods. The system utilizes specific gas mixtures and optimized nozzle designs to create a more concentrated plasma arc. This results in superior cut quality and improved precision compared to conventional plasma systems, which use basic gas configurations and standard nozzle designs.
Cut Quality Parameters
The distinction in cut quality between these technologies is substantial. HD plasma cutting produces exceptionally smooth cut surfaces with minimal dross formation and superior edge quality. These systems typically achieve squareness deviation less than 2 degrees, while conventional plasma cutting often results in more pronounced beveling and requires additional finishing operations.
Operational Precision
HD plasma cutting in Houston facilities demonstrate superior control over crucial operational parameters. These systems maintain precise control over factors such as:
- Arc voltage stability
- Gas flow dynamics
- Torch height control
- Pierce point accuracy
Conventional systems, while functional, operate with broader parameter ranges, leading to more variable results.
Material Processing Capabilities
Both technologies handle various material thicknesses, but their optimal processing ranges differ significantly. HD plasma cutting operations excel in processing materials from thin gauge up to 2 inches thick, maintaining consistent quality throughout this range. Conventional systems show optimal performance primarily in medium thickness ranges, with more variable results at extreme thicknesses.
Production Efficiency Analysis
Speed and productivity factors reveal significant differences between these technologies. HD plasma cutting systems typically achieve higher cutting speeds, particularly in materials under 1 inch thick. The reduced need for secondary operations further enhances overall productivity compared to conventional methods.
Operating Cost Structure
A comprehensive cost analysis reveals distinct patterns between these technologies. While HD plasma cutting in Houston requires higher initial investment and specialized consumables, the improved cut quality and reduced secondary processing often justify these costs. Conventional systems offer lower initial costs but may incur higher operational expenses due to increased post-processing requirements.
Consumable Life and Management
Consumable components show different wear patterns between these technologies. HD systems typically demonstrate longer consumable life due to optimized arc characteristics and improved cooling designs. Conventional systems often require more frequent consumable replacements, affecting both maintenance schedules and operational costs.
Quality Control Measures
Quality assurance procedures differ significantly between these cutting methods. HD plasma cutting systems incorporate advanced monitoring and control systems that maintain consistent cut quality. Conventional systems typically require more frequent operator intervention and adjustment to maintain acceptable quality levels.
Application-Specific Considerations
Different industrial applications benefit variously from these technologies. HD plasma cutting in Houston proves particularly valuable in applications requiring high precision and minimal secondary operations. Conventional plasma cutting remains effective for applications where moderate precision meets project requirements and cost constraints are primary considerations.
Conclusion
This comparative analysis demonstrates the distinct advantages and limitations of HD plasma cutting versus conventional plasma cutting technologies. The choice between these systems depends on specific application requirements, including precision needs, production volume, and economic considerations. Understanding these differences enables informed decision-making in selecting the appropriate technology for specific manufacturing requirements.