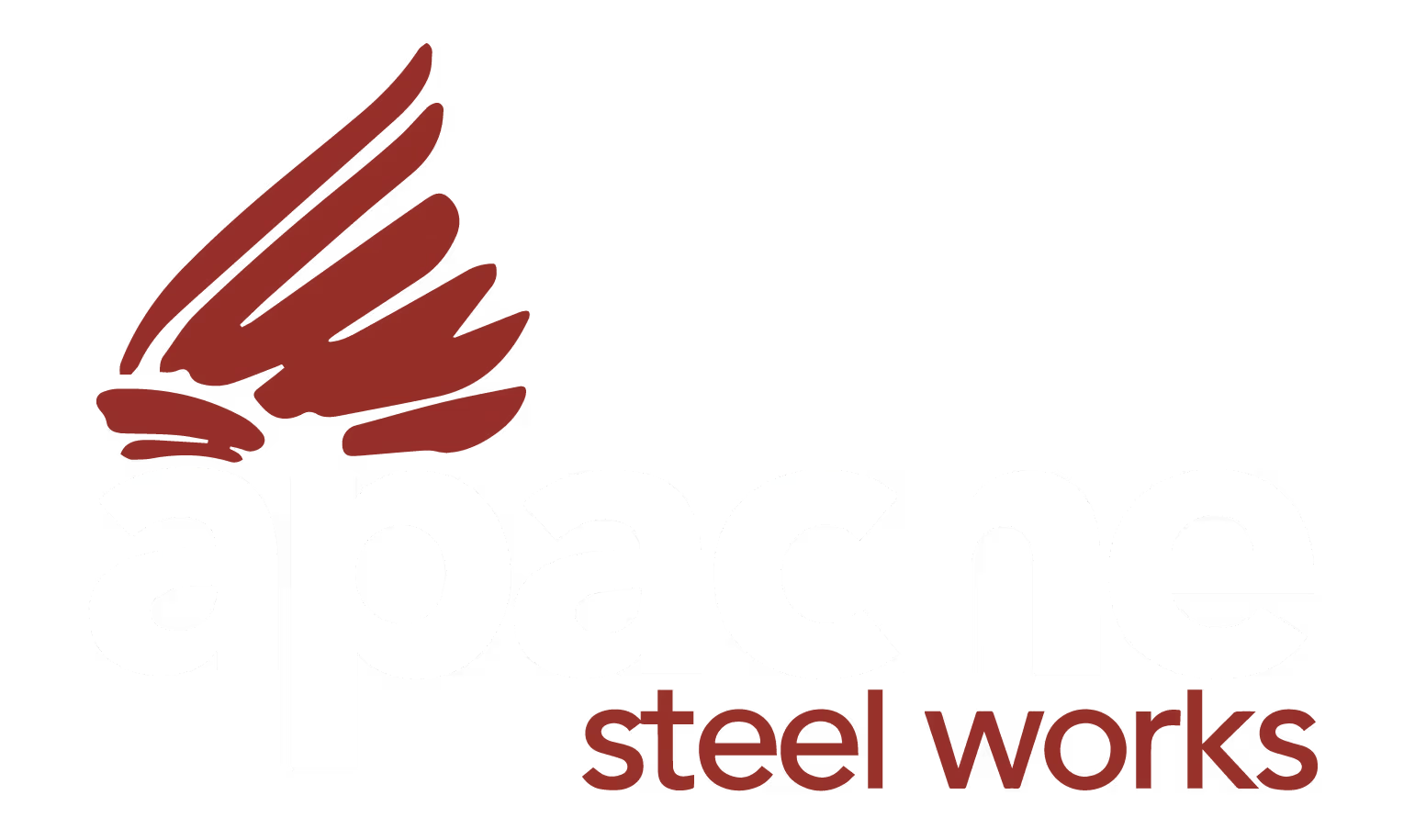
Plate Processing Company
HD Plasma Cutting: Precision Technology for Modern Manufacturing
HD Plasma Cutting: Precision Technology for Modern Manufacturing
Manufacturing precision requires sophisticated cutting technologies, and HD plasma cutting represents a remarkable solution for industries seeking accurate and efficient metal processing. Unlike traditional cutting methods, HD plasma cutting delivers exceptional performance that transforms how manufacturers approach material fabrication.
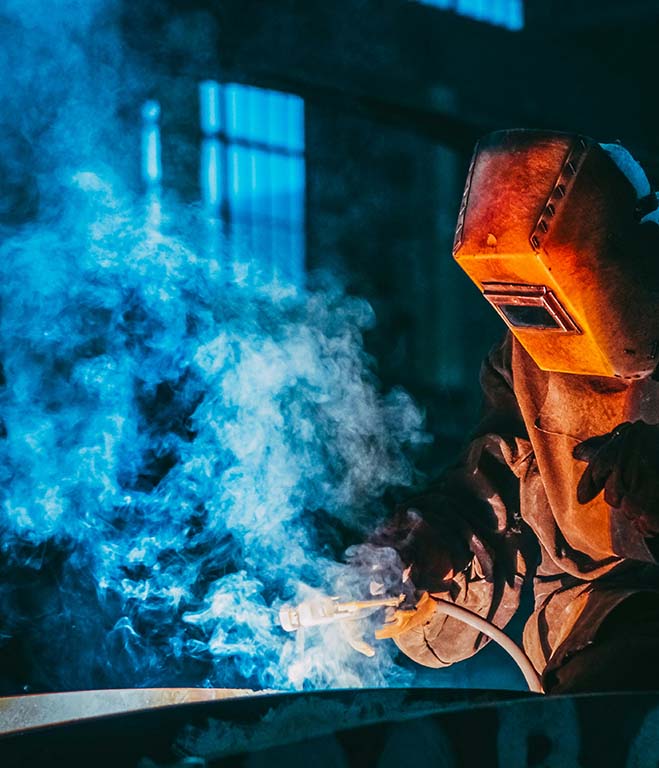
The Science Behind HD Plasma Cutting
Plasma cutting utilizes superheated electrical gas streams to slice through conductive materials with remarkable precision. The process involves creating an electrically conductive channel of plasma that melts and removes material instantaneously. HD plasma cutting in Houston has become particularly renowned for its ability to handle complex geometrical designs with minimal material waste and exceptional edge quality.
Technical Mechanics of Plasma Cutting Process
The plasma cutting mechanism operates through a sophisticated electrical arc generation process. Compressed gas is forced through a narrow opening while an electrical arc transforms the gas into a plasma state. This plasma stream reaches temperatures exceeding 20,000 degrees Fahrenheit, enabling it to slice through metal sheets with unprecedented accuracy and speed.
Material Compatibility and Performance
HD plasma cutting works effectively with various conductive metals including steel, aluminum, copper, and brass. The technology demonstrates exceptional versatility in handling different material thicknesses, typically ranging from thin sheets to substantial metal plates. HD plasma cutting in Houston manufacturing facilities has proven particularly effective for industries requiring precise metal fabrication.
Precision and Cut Quality Considerations
Cutting quality depends on multiple factors such as gas pressure, electrical current, nozzle design, and electrode configuration. Modern HD plasma cutting systems incorporate advanced computer numerical control (CNC) technologies that ensure consistent cutting paths and minimal deviation. Manufacturers can achieve intricate designs with tolerances as tight as 0.010 inches, representing a significant advancement in metalworking precision.
Economic and Operational Advantages
Plasma cutting offers substantial economic benefits compared to traditional cutting methods. The technology reduces material waste, minimizes secondary processing requirements, and accelerates production timelines. Companies utilizing HD plasma cutting can expect lower operational costs, faster project completion, and improved overall manufacturing efficiency.
Equipment and Technical Specifications
Professional HD plasma cutting systems incorporate multiple sophisticated components. These include high-frequency power supplies, precision gas flow controllers, advanced cooling mechanisms, and robust mechanical frameworks. Specialized nozzle designs help maintain consistent plasma stream characteristics, ensuring uniform cutting performance across different material types and thicknesses.
Safety and Operational Protocols
Implementing HD plasma cutting requires comprehensive safety protocols. Operators must wear appropriate personal protective equipment, including flame-resistant clothing, welding helmets, and specialized gloves. Proper ventilation, fire prevention measures, and thorough equipment maintenance are crucial for safe and effective plasma cutting operations.
Industrial Applications
HD plasma cutting finds applications across diverse industrial sectors including automotive manufacturing, aerospace engineering, construction equipment production, and metal fabrication. Specialized industries like shipbuilding and architectural metalwork rely heavily on the precision and efficiency of advanced plasma cutting technologies.
Complex Cutting Capabilities
Beyond standard straight-line cutting, modern HD plasma cutting systems can execute complex geometric shapes, curved designs, and intricate patterns. Computer-controlled machines enable manufacturers to translate complex digital designs into precise physical components with minimal human intervention.
Maintenance and Performance Optimization
Regular maintenance ensures consistent plasma cutting performance. This includes periodic electrode replacement, nozzle cleaning, and calibration of electrical and gas systems. Proper maintenance helps prevent performance degradation and extends equipment operational lifespan.
The world of metal fabrication continues to evolve, with HD plasma cutting representing a pinnacle of precision engineering. By understanding its technical nuances and operational advantages, manufacturers can leverage this technology to achieve unprecedented levels of manufacturing excellence.