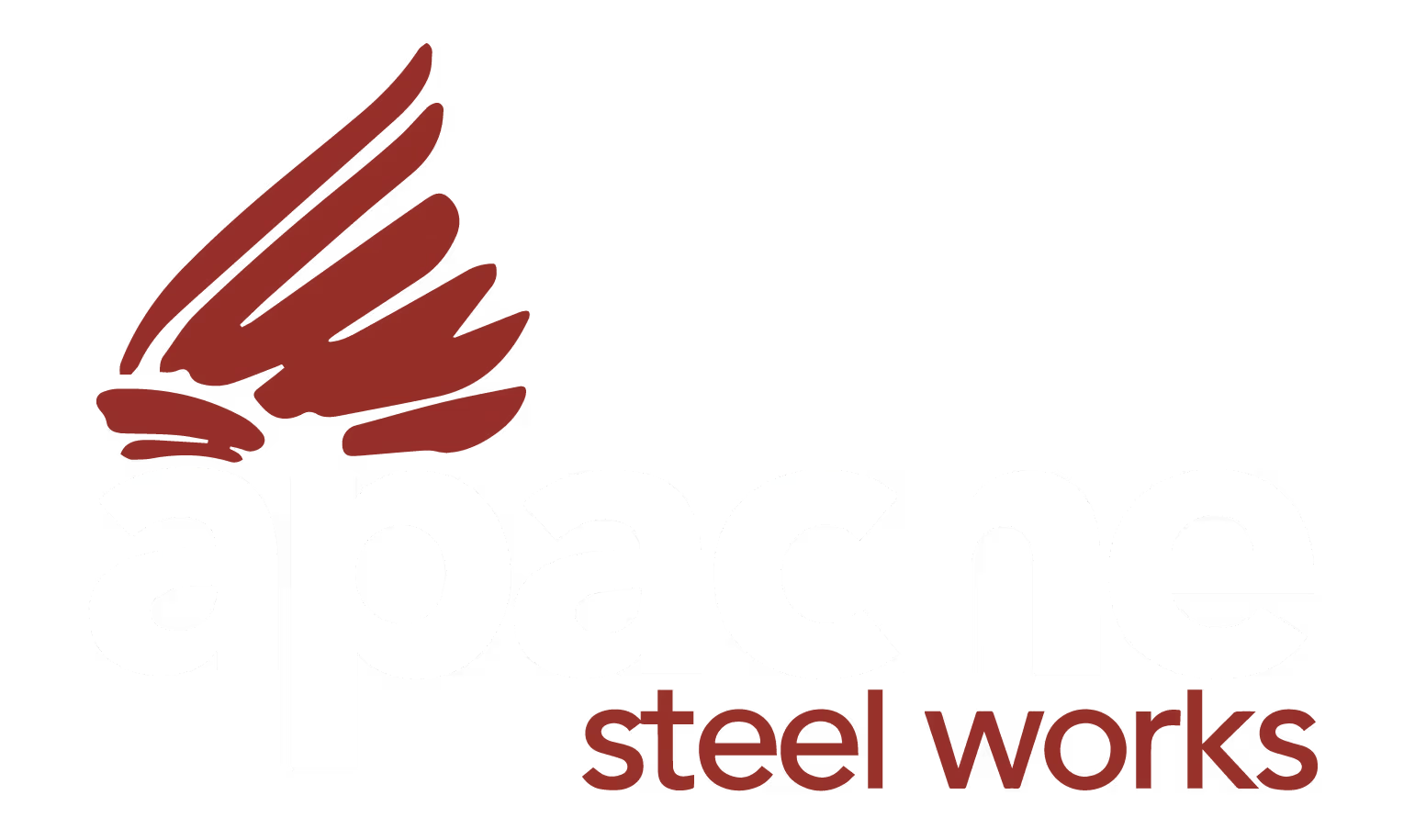
Plate Processing Company
Difference Between Plate Forming and Plate Fabrication
Difference Between Plate Forming and Plate Fabrication
Metal plate processing encompasses two distinct yet complementary processes: plate forming and plate fabrication. While these terms are often used interchangeably, they represent different aspects of metal plate processing. As any plate forming specialist in Houston would confirm, understanding these differences is crucial for selecting the appropriate process for specific project requirements.
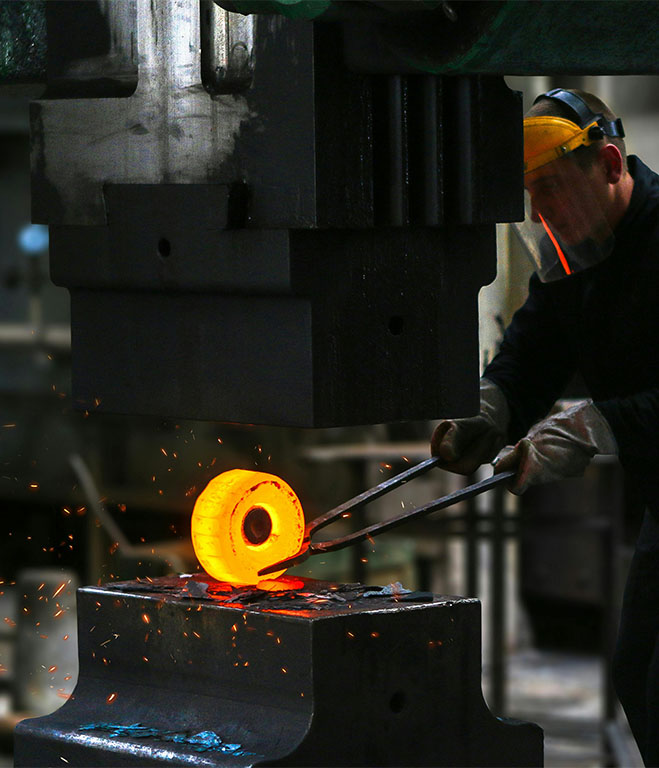
Basic Definition and Scope
Plate forming focuses specifically on changing the shape of metal plates without altering their thickness or fundamental structure. A plate forming specialist in Houston typically employs various techniques to bend, roll, or shape plates into specific geometries while maintaining material integrity. In contrast, plate fabrication encompasses a broader range of operations, including cutting, joining, and assembly processes.
Equipment and Tools
The equipment used in each process differs significantly. Plate forming requires specialized machinery like press brakes, plate rolls, and forming dies. Every plate forming specialist relies on these precision tools to achieve accurate bends and curves. Fabrication equipment, however, includes a wider array of tools such as cutting machines, welding equipment, and assembly fixtures.
Process Methodology
Plate forming follows a specific methodology focused on controlled deformation. The process involves calculating bend allowances, determining forming sequences, and maintaining precise control over forming pressures. Fabrication processes, alternatively, involve multiple steps that may include cutting patterns, preparing edges, and joining components through welding or mechanical fastening.
Material Considerations
When consulting a plate forming specialist in Houston, material properties play a crucial role in determining forming parameters. Factors like yield strength, ductility, and thickness directly impact forming capabilities. Fabrication processes must consider additional material properties related to cutting, welding, and assembly requirements.
Quality Control Parameters
Quality control in plate forming focuses primarily on geometric accuracy, springback compensation, and surface finish preservation. A skilled plate forming specialist in Houston employs various measurement techniques to ensure formed parts meet specifications. Fabrication quality control encompasses additional aspects like weld quality, assembly tolerance, and overall structural integrity.
Technical Expertise Required
Both processes require distinct technical expertise. Plate forming demands deep understanding of metal behavior during bending and forming operations. Fabrication requires broader knowledge encompassing multiple processes like cutting, welding, and assembly techniques. These different skill sets often lead to specialization among technicians.
Time and Cost Factors
Time and cost considerations differ between these processes. Plate forming typically involves shorter processing times for individual operations but may require more setup time. Fabrication projects often involve multiple steps and longer overall processing times, impacting project timelines and costs differently.
Application Areas
While both processes serve manufacturing needs, their applications differ. Plate forming excels in creating specific shapes like cylinders, cones, and complex bends. Fabrication proves essential when projects require complete assemblies or structures combining multiple components and joining methods.
Project Planning Considerations
Planning requirements vary between forming and fabrication projects. A plate forming specialist in Houston typically focuses on forming sequence optimization and tool selection. Fabrication planning must account for multiple process steps, material flow, and assembly sequences, making it more complex in many cases.
Conclusion
Understanding the distinctions between plate forming and plate fabrication helps in selecting the appropriate process for specific project requirements. While both processes play vital roles in metal plate processing, their different characteristics, requirements, and applications make them uniquely suited for different aspects of manufacturing projects. This understanding enables better project planning and execution, ultimately leading to more successful outcomes in metal plate processing projects.