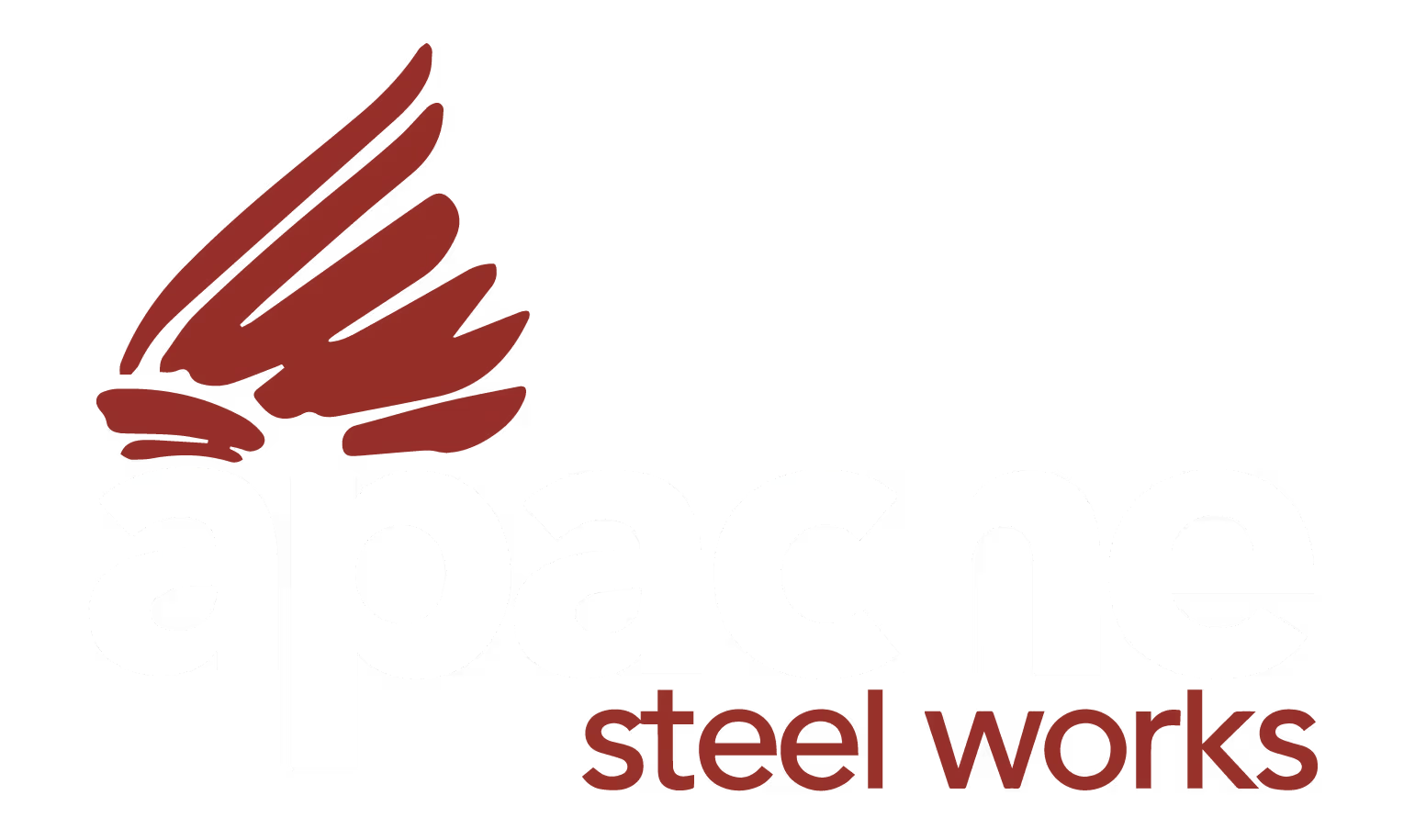
Plate Processing Company
Best Practices for Manual Beveling in Houston Welding Projects
Best Practices for Manual Beveling in Houston Welding Projects
Beveling is an important part of the welding process that helps ensure proper penetration and a strong weld. When done correctly, beveling allows the weld to fuse with the base metal for maximum strength. This is especially important for welding projects in Houston, where heat and humidity can impact welding results.
If you're taking on a welding project in Houston, here are some best practices to follow for manual beveling for welding in Houston:
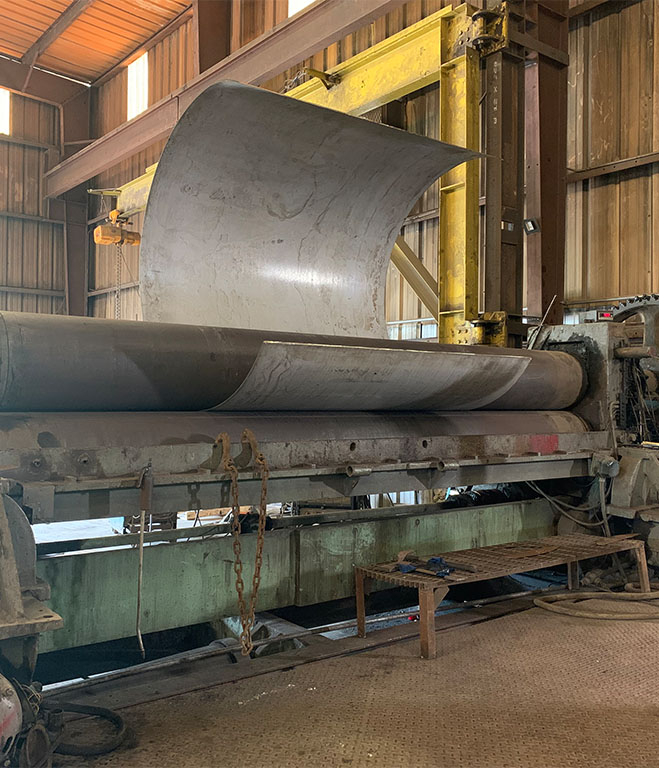
Prepare Your Materials
The first step is ensuring you have the right materials and tools for beveling. You'll need a grinding wheel or file to manually shape the bevel. Make sure your steel is clean and free of rust, paint or other coatings that can contaminate the weld. Wear proper protective equipment, like gloves and eye protection, when beveling.
Determine the Correct Bevel Angle
The angle of the bevel is key - too shallow and the weld won't penetrate deeply enough; too steep and you may burn through the metal. For steel, a 45 degree bevel is commonly used for thicknesses up to 1 inch. You can decrease the angle slightly for thinner materials. When in doubt, do a quick test weld first to dial in the right angle.
Allow for Proper Root Opening
The root opening, or separation between the edges of the beveled metal, is also important for penetration. The gap should be wider for thicker steel so that the weld can fully fuse with the base metal. A rule of thumb is to allow 1/16 inch of root opening per 1/8 inch of steel thickness.
Grind a Smooth, Even Bevel
Use steady, even motions when filing or grinding to create a smooth bevel without waves or uneven edges. This allows for consistent weld penetration. Any pitting or roughness can lead to weak spots.
Bevel Both Pieces to Be Joined
When butt welding two pieces of steel, both edges should be beveled to allow full fusion between the metals. Grinding only one piece leaves less surface area for the weld to adhere correctly. Matching bevels ensure proper alignment.
Follow the Exact Bevel Specifications
For structural welds or critical applications, be sure to follow the exact bevel specifications called out in the welding procedure specification (WPS). The WPS provides the approved bevel angle, root opening, and groove configuration for the specific welding job. Straying from the WPS can compromise weld integrity.
Allow a Landing Area
When possible, allow for a small, flat "landing area" at the top of the bevel to support the welding torch. This helps prevent slipping and inconsistent welding. A landing area of 1/16 to 1/8 inch is ideal.
Keep Things Square
Maintain square edges and proper joint alignment when beveling multiple pieces to be joined. The beveled edges should match up evenly, with no gaps between them, to prevent cracks or weaknesses in the final weld. Tack weld pieces first if needed.
Preheat Properly
With certain metals, preheating before welding is required to slow cooling and prevent cracks. Follow specific preheat guidelines for the metal alloy you're welding. Temperature sticks are useful for tracking preheat times.
Watch Your Technique
Move the grinder or file at a steady angle when beveling to create an even surface. Avoid rocking the tool back and forth. For longer edges, bevel a couple inches at a time, working your way along the joint to avoid fatigue and inconsistencies. A straightedge tool can be used to check flatness.
By following these key tips for manual bevel preparation, you can help ensure your Houston welding projects have strong, lasting welds that withstand the region's humid environment. Proper preparation for beveling for welding in Houston takes time but is worth the investment for quality, safety and durability. With the right technique, you can bevel like a pro.