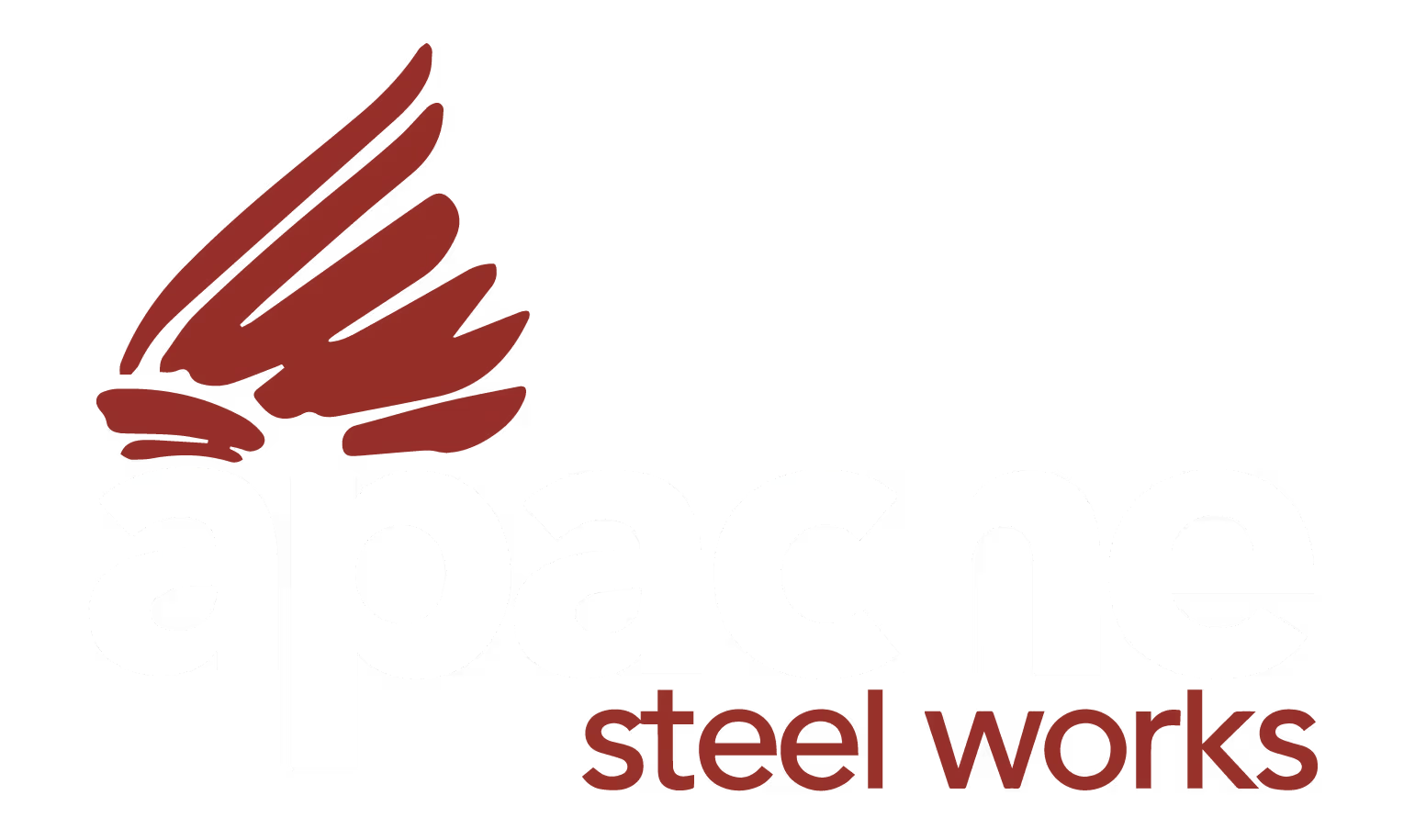
Plate Processing Company
Basic Terminologies Used by Plate Rolling Professionals and Their Meaning
Basic Terminologies Used by Plate Rolling Professionals and Their Meaning
When you step into a plate rolling workshop, you might hear new words you may have never heard before. Plate rolling professionals in Houston and around the globe use specific terms that can sound like a foreign dialect to others. But don't worry - we're here to help you understand some of the most commonly used words by plate rolling professionals.
Whether you're considering a career in this field or just curious about the process, this guide will help you get familiar with the lingo.
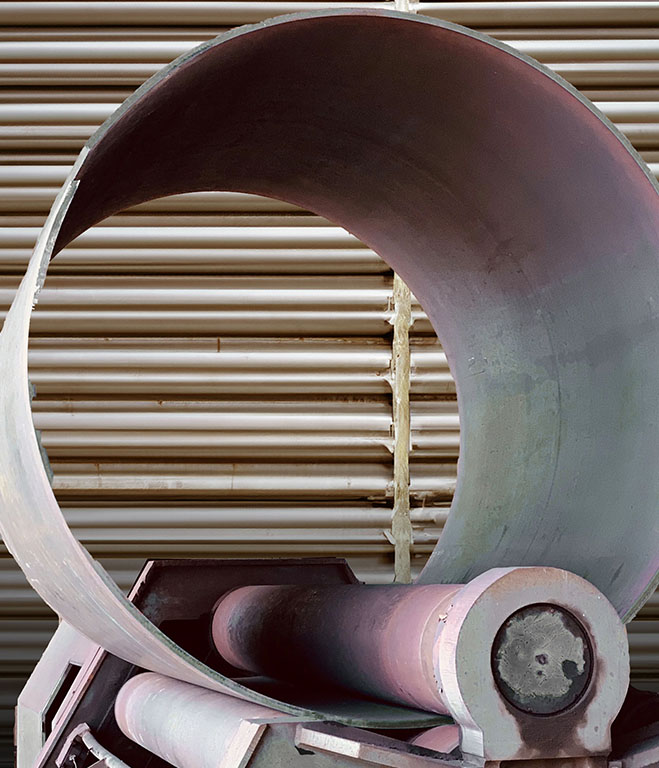
- Plate Rolling
Plate rolling is the process of bending flat metal plates into cylindrical or conical shapes. It's a crucial technique used in manufacturing everything from storage tanks to wind turbine towers.
- Roller
Rollers are the cylindrical components that apply pressure to the metal plate, causing it to bend. Plate rolling professionals often work with machines that have three or four rollers.
- Pre-bending
Before the main rolling process begins, the edges of the plate need to be bent. This initial bending is called pre-bending. It's a critical step that ensures the final product has a uniform circular shape.
- Crowning
In plate rolling, crowning refers to the slight curve given to the rollers. This compensates for the tendency of the plate to bow in the middle during rolling.
- Spring-back
After the plate is rolled, it has a tendency to partially unroll due to the metal's elasticity. This phenomenon is called spring-back. Experienced plate rolling professionals know how to account for this when setting up their machines.
- Yield Strength
This term refers to the amount of stress a metal can handle before it starts to deform permanently. It's an important factor that plate rolling professionals consider when choosing rolling parameters.
- Work Hardening
As metal is bent and shaped, it can become stronger and harder. This process is called work hardening. It's both a challenge and a tool in plate rolling, depending on the desired outcome.
- Neutral Axis
Imagine a line running through the center of the plate's thickness. This line, which experiences neither compression nor tension during bending, is called the neutral axis.
- Minimum Inside Radius
This is the smallest radius to which a plate can be safely rolled without damaging the material. It's usually expressed as a multiple of the plate thickness.
- Pyramidal Plate Roll
This is a type of plate rolling machine with three rollers arranged in a pyramid shape. It's commonly used for rolling thicker plates.
- Pinch Plate Roll
Unlike the pyramidal roll, a pinch plate roll has two main rollers that "pinch" the plate, with a third roller on top for adjusting the curve.
- Conical Rolling
Sometimes, plate rolling professionals need to create cone shapes rather than cylinders. This process is called conical rolling and requires special techniques and often specialized machinery.
- Straightening
After welding or other processes, rolled plates might develop some unwanted curvature. Straightening is the process of correcting these imperfections to achieve the desired shape.
- Plate Thickness Tolerance
This refers to the acceptable variation in plate thickness. It's crucial for ensuring the final product meets specifications.
- Dimensional Tolerance
Similar to thickness tolerance, this term refers to the acceptable variation in the overall dimensions of the rolled product.The professionals, who work in this field, including plate rolling professionals in Houston, use their knowledge of these concepts every day to create the cylindrical and conical shapes that are essential in many industries.From massive storage tanks that hold fuel for entire cities, to the graceful curves of modern architecture, the work of plate rolling professionals touches many aspects of our lives. Their expertise in manipulating metal, understanding its properties, and shaping it to precise specifications is truly remarkable.Next time you see a large metal tank or a curved piece of industrial equipment, you'll have a better understanding of the terminology and processes that went into creating it. Remember, while these terms are used globally, the specific techniques and approaches may vary.